レーザーによる軸芯出し方法:精度と効率のベストプラクティス
2024/08/08
産業機械の最適な性能を維持するためには、正確な軸芯出しが不可欠です。従来の手法では時間がかかり、精度にも限界がありましたが、レーザーを用いた軸芯出し方法はこれを一変させました。ミクロン単位の精度で機械の軸芯を調整でき、摩擦やエネルギーロスを最小限に抑えることができます。本記事では、レーザー技術を活用した軸芯出し方法のベストプラクティスについて詳しく解説します。
目次
レーザー技術の進化が軸芯出し方法にもたらす革新
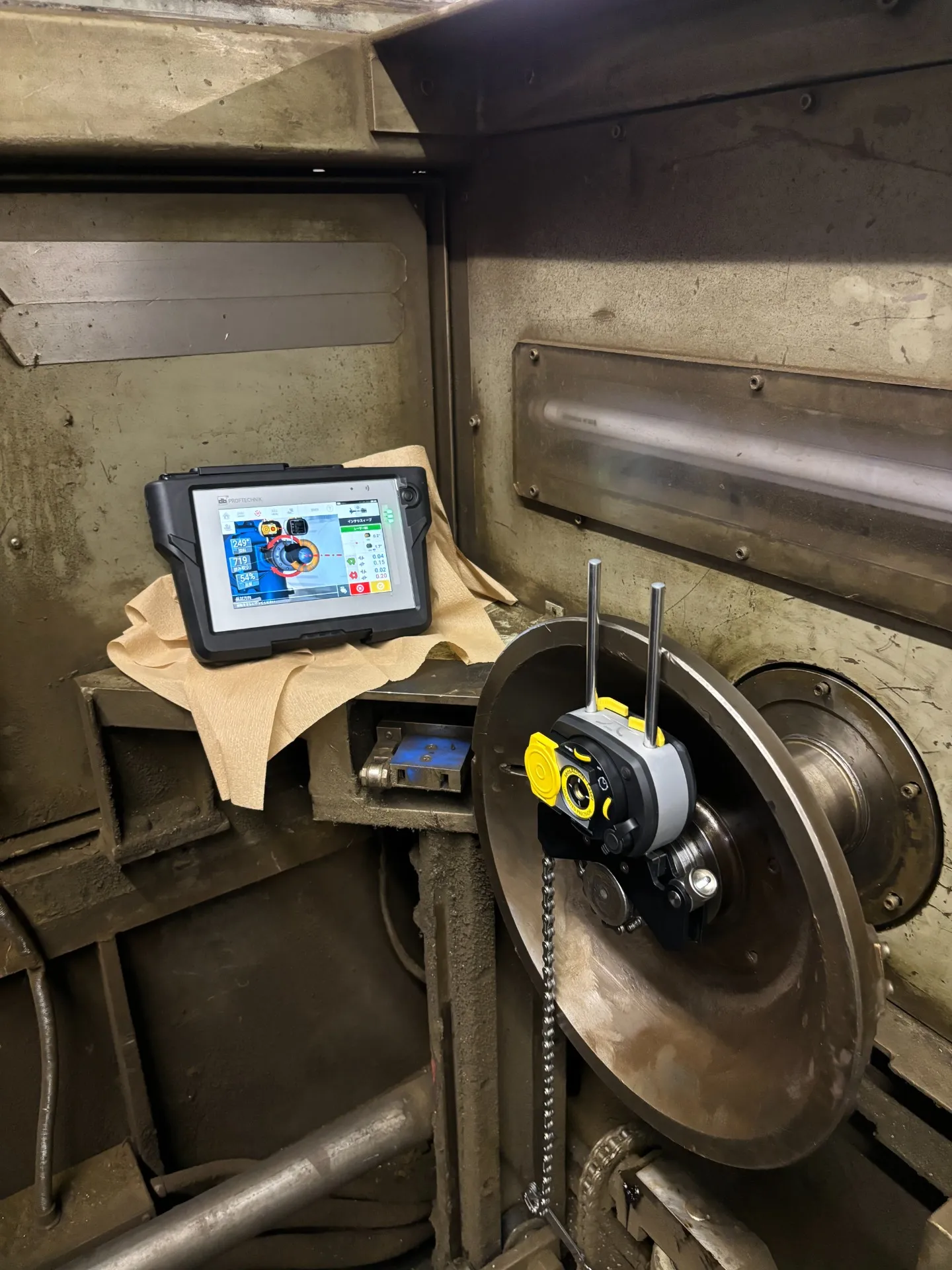
レーザー技術の基本原理
レーザー技術は、光の増幅によって高い指向性と強度を持つ光を生成する技術です。レーザーは、特定の波長の光子を共鳴器内で増幅し、その結果として非常に直線的で集中した光束を作り出します。軸芯出し方法においては、この直線性と高精度な測定能力が非常に重要であり、機械の軸芯のズレをミクロン単位で検出することが可能です。レーザー技術の基本原理を理解することで、なぜこの技術が軸芯出しに有効であるかが明確になります。
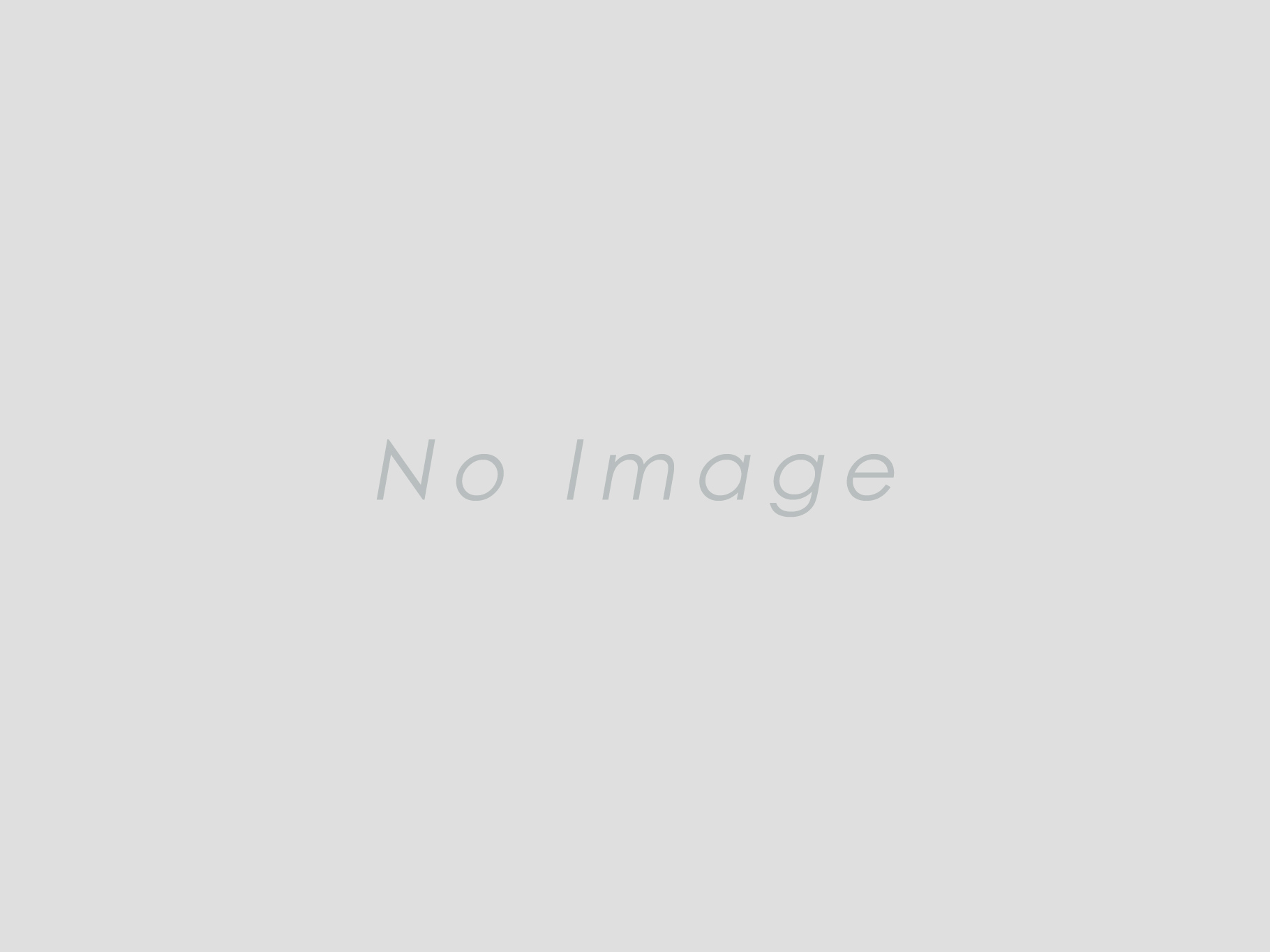
軸芯出しの従来手法との比較
従来の軸芯出し方法は、機械的なゲージやダイヤルインジケータを用いて行われることが一般的でした。これらの方法では、微細なズレを検出するのが難しく、作業に時間がかかるという欠点がありました。しかし、レーザーを用いた軸芯出し方法では、光の直線性と高精度な測定能力によって、従来の手法では達成できなかった精度と効率が得られます。特に、レーザー技術は軸芯のズレをリアルタイムで視覚的に確認できるため、修正作業が迅速かつ正確に行われます。
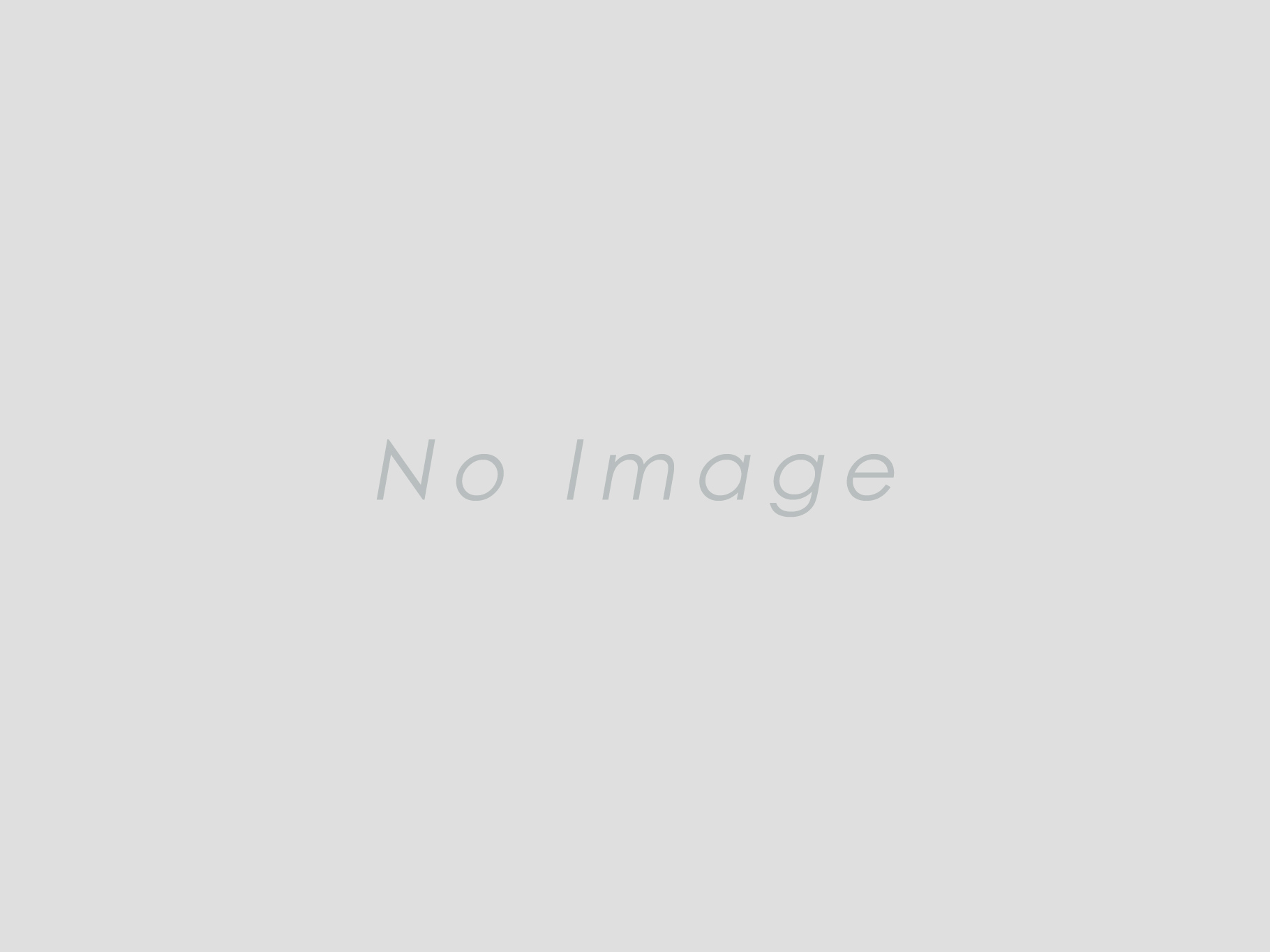
レーザー技術導入の利点
レーザーによる軸芯出し方法の導入は、数多くの利点をもたらします。まず、ミクロン単位での高精度な調整が可能となり、機械の振動を劇的に減少させることができます。これは、摩耗やエネルギーロスを最小限に抑えるため、機械の寿命延長にも寄与します。また、従来の手法に比べて作業時間が大幅に短縮され、効率的な運用が実現されます。さらに、操作が簡単で、専門知識がなくても扱えるため、現場の作業者の負担も軽減されます。このように、レーザー技術の導入は全体的な生産性向上に大いに貢献します。
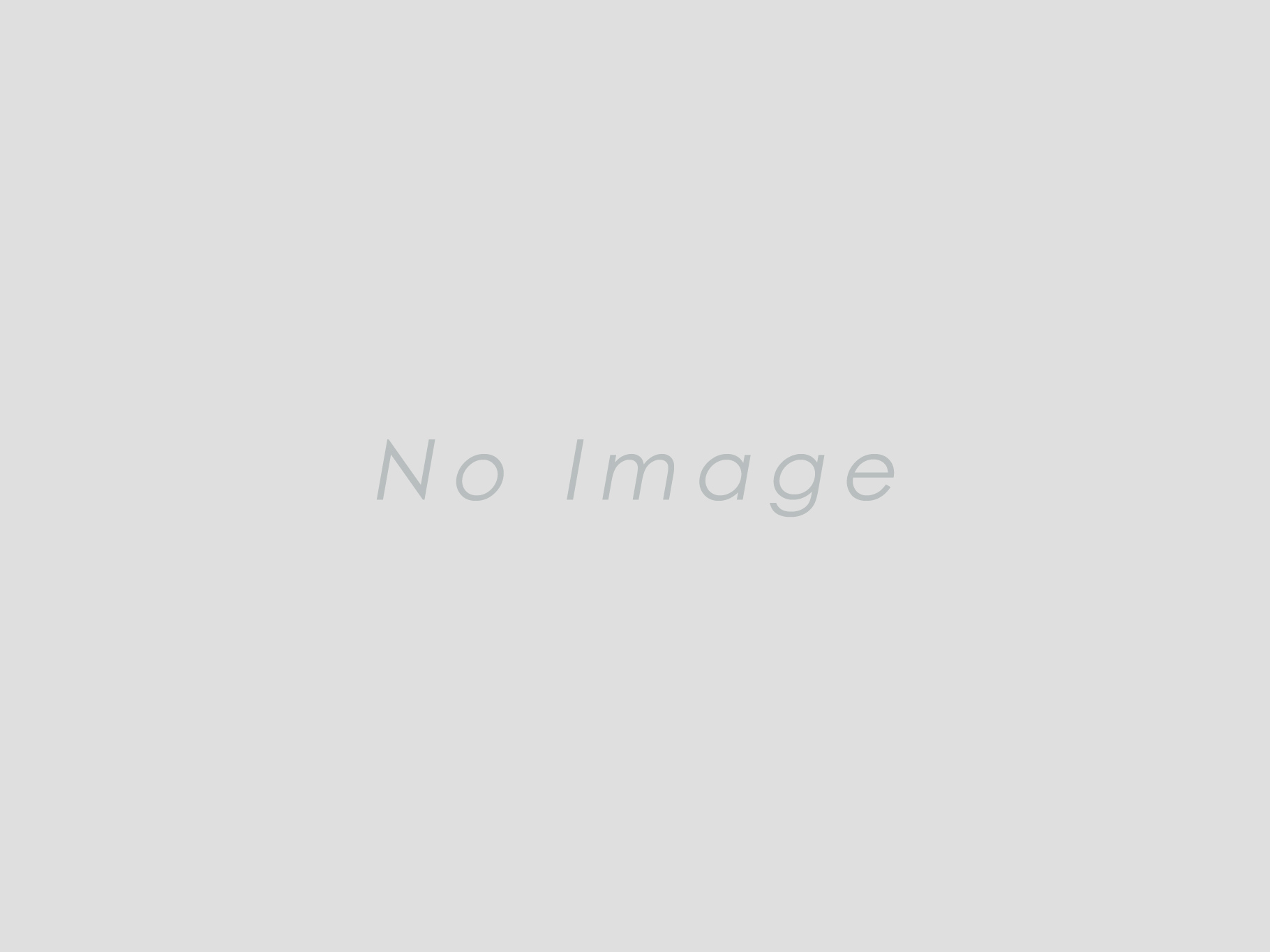
産業機械におけるレーザーの応用
産業機械におけるレーザー技術の応用は、軸芯出し以外にも多岐にわたります。例えば、高精度な切断や溶接においてもレーザーはその威力を発揮します。レーザーによる軸芯出し方法は、特に大型の機械設備や複雑な機構を持つ装置において、その効果が顕著です。これにより、機械の稼働率が向上し、不良品の発生率も低減されます。また、リアルタイムでの測定と調整が可能なため、突発的なトラブルにも迅速に対応できます。レーザー技術は、産業界において不可欠な存在となりつつあります。
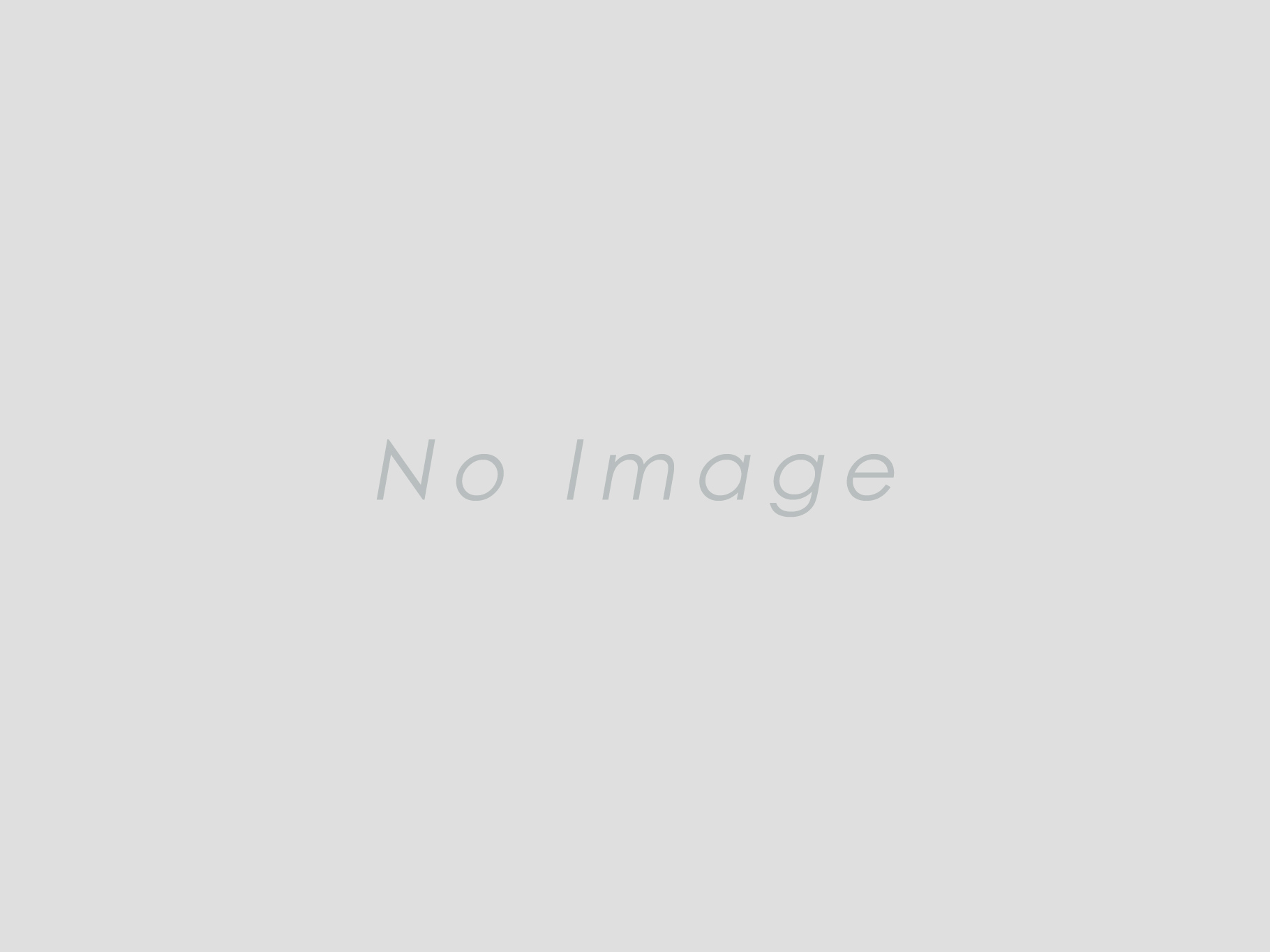
革新的なレーザー技術の最新トレンド
レーザー技術は日々進化を遂げており、軸芯出し方法にも革新的な進展が見られます。最新のレーザー技術は、より高い精度と迅速な作業を実現するために、従来の手法を凌駕しています。例えば、自動キャリブレーション機能を備えたレーザー軸芯出し器が登場し、手動での調整作業を大幅に削減しました。さらに、スマートフォンやタブレットと連携することで、リアルタイムでデータを確認しながら微調整が可能となり、作業効率が一層向上しました。これらの最新トレンドは、産業界に新たな可能性をもたらし、今後の技術開発においても期待が高まります。このシリーズを通じて、レーザー技術の未来についてご理解いただけたでしょうか。次回も新しいテーマでお会いしましょう。
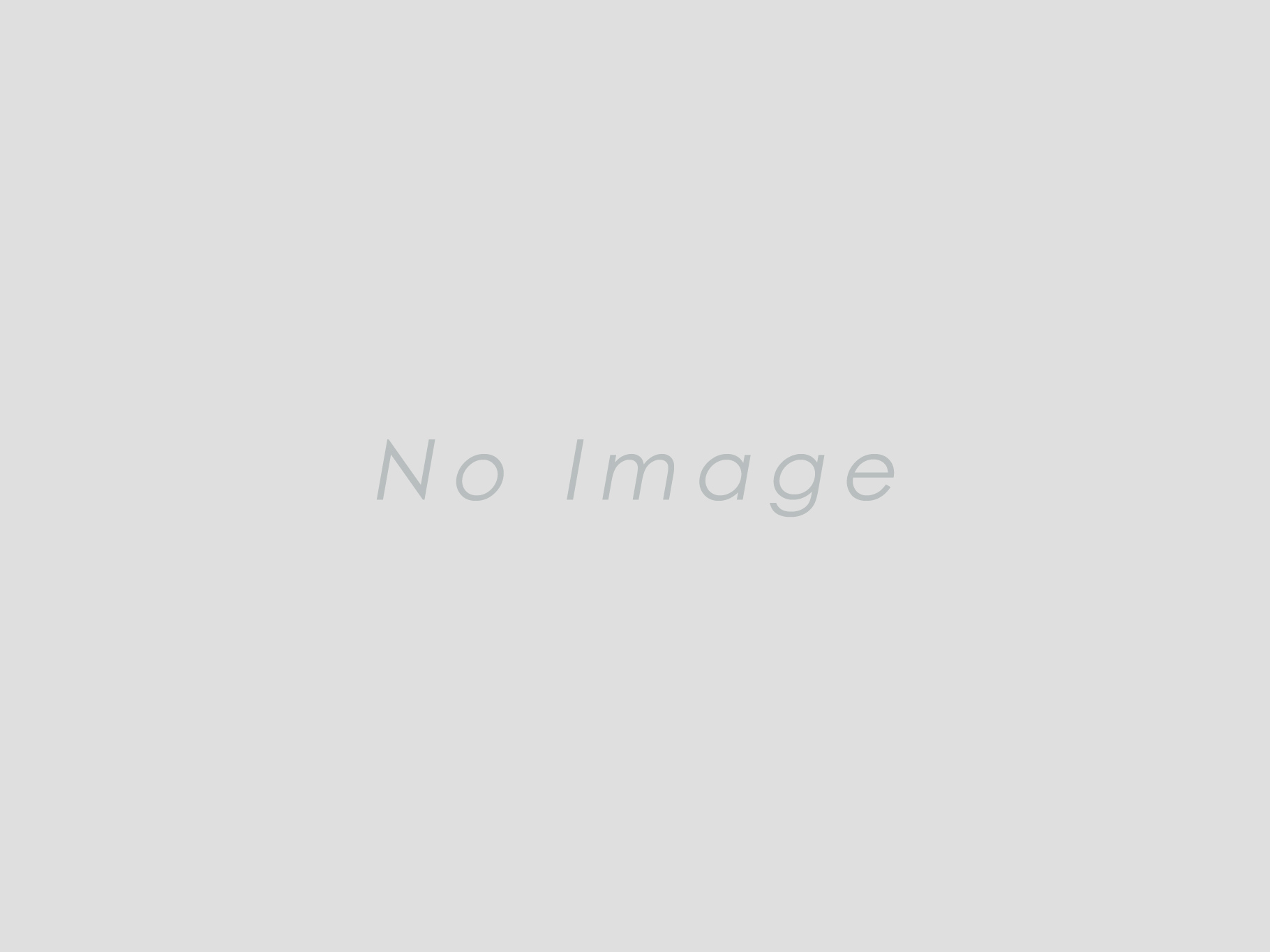
レーザーによる軸芯出しの事例紹介
レーザー技術を活用した軸芯出しの実例をいくつかご紹介します。ある製造工場では、従来の手法で行われていた軸芯出し作業に比べ、レーザー軸芯出し器を導入することで作業時間を50%削減することに成功しました。さらに、ミクロン単位の精度での調整が可能となり、機械の振動が大幅に減少し、結果としてエネルギーロスも最小限に抑えられました。また、定期的なメンテナンスが容易となり、機械の寿命が延びる効果も確認されています。レーザー技術の導入は、効率と精度の両方で大きなメリットをもたらすことが明らかです。これまでのシリーズを通じて、レーザーによる軸芯出し方法の重要性とその利点についてご理解いただけたと思います。次回もお楽しみに。
軸芯出し方法の新時代:レーザーを活用した精度の飛躍
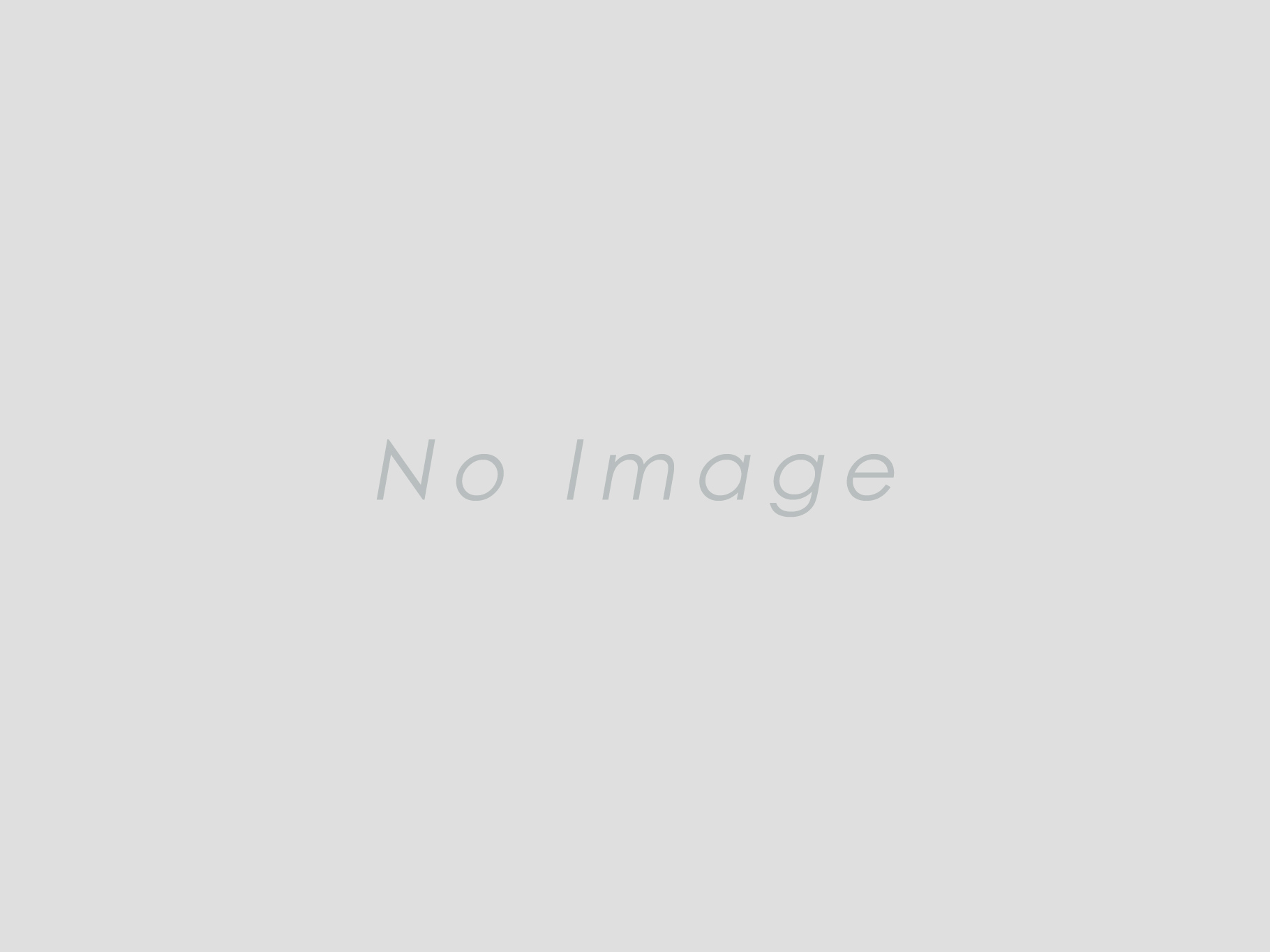
レーザー軸芯出しの精度の秘密
レーザー軸芯出しの精度の秘密は、その特殊な測定技術にあります。レーザー光は直進性が高く、微細なズレも正確に検出できるため、ミクロン単位での軸芯調整が可能です。レーザー軸芯出し器は、インテリジェントなセンサーを搭載しており、リアルタイムで測定結果を表示します。この精密な測定は、機械の振動を最小限に抑え、エネルギーロスを減少させることができます。また、レーザー技術は非接触型であるため、測定対象に物理的な負荷をかけずに高精度な軸芯出しが実現できます。このような高精度の測定能力により、産業機械の性能を最大限に引き出すことができるのです。
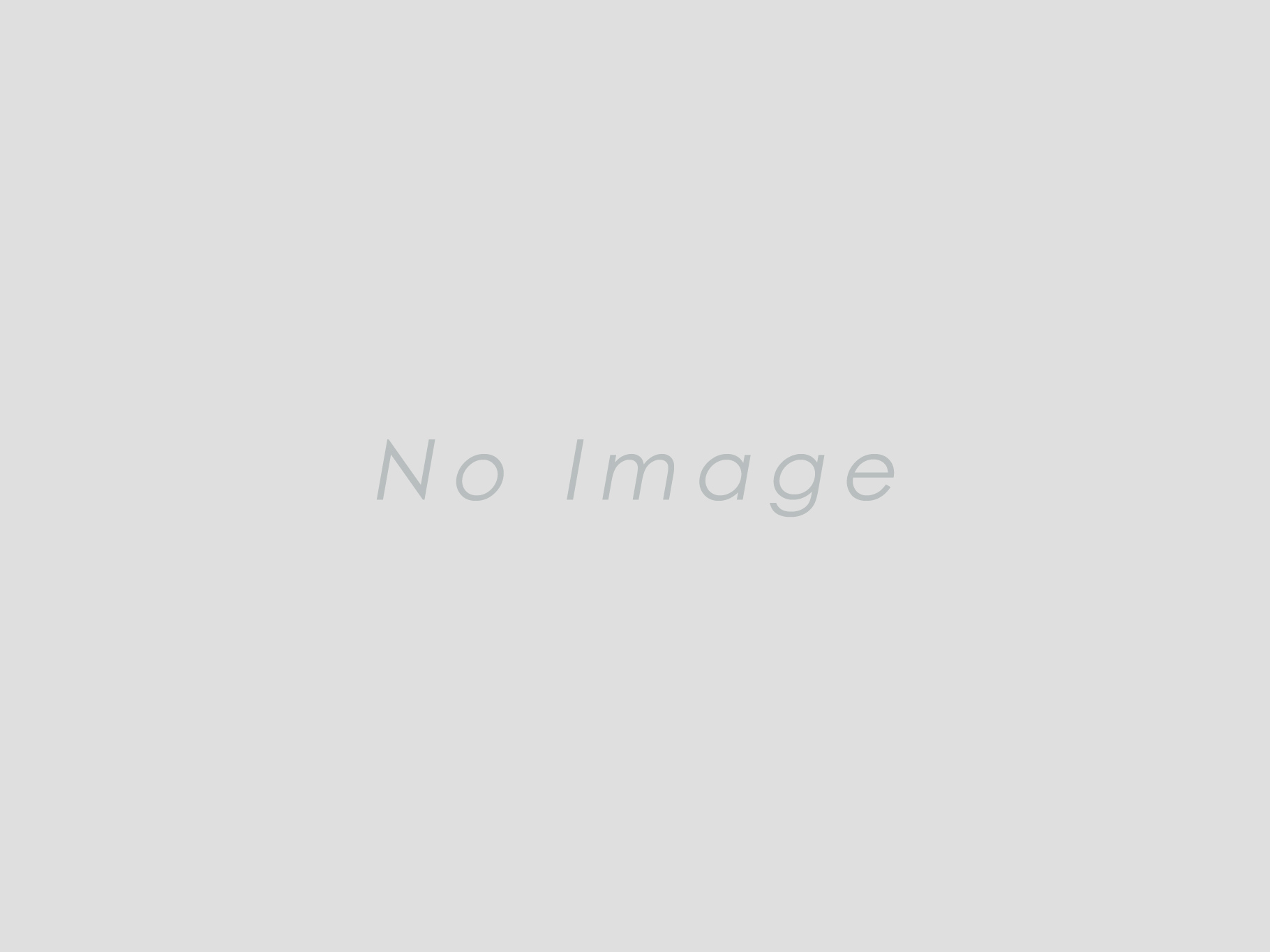
従来手法の限界とレーザー技術の優位性
従来の軸芯出し方法は、目視や機械的な計測器を用いることが一般的でした。しかし、これらの手法では微細なズレを正確に検出することが難しく、結果として精度が低くなる傾向があります。また、手動の調整は時間がかかり、作業効率も低いです。一方、レーザー軸芯出し技術はこれらの限界を克服します。レーザー光の高い直進性と精密なセンサーにより、微細なズレも正確に検出でき、ミクロン単位の調整が可能です。この高精度の測定技術により、機械の振動を大幅に減少させ、エネルギーロスを最小限に抑えることができます。さらに、レーザー軸芯出しは短時間での作業が可能であり、生産性と効率が大幅に向上します。
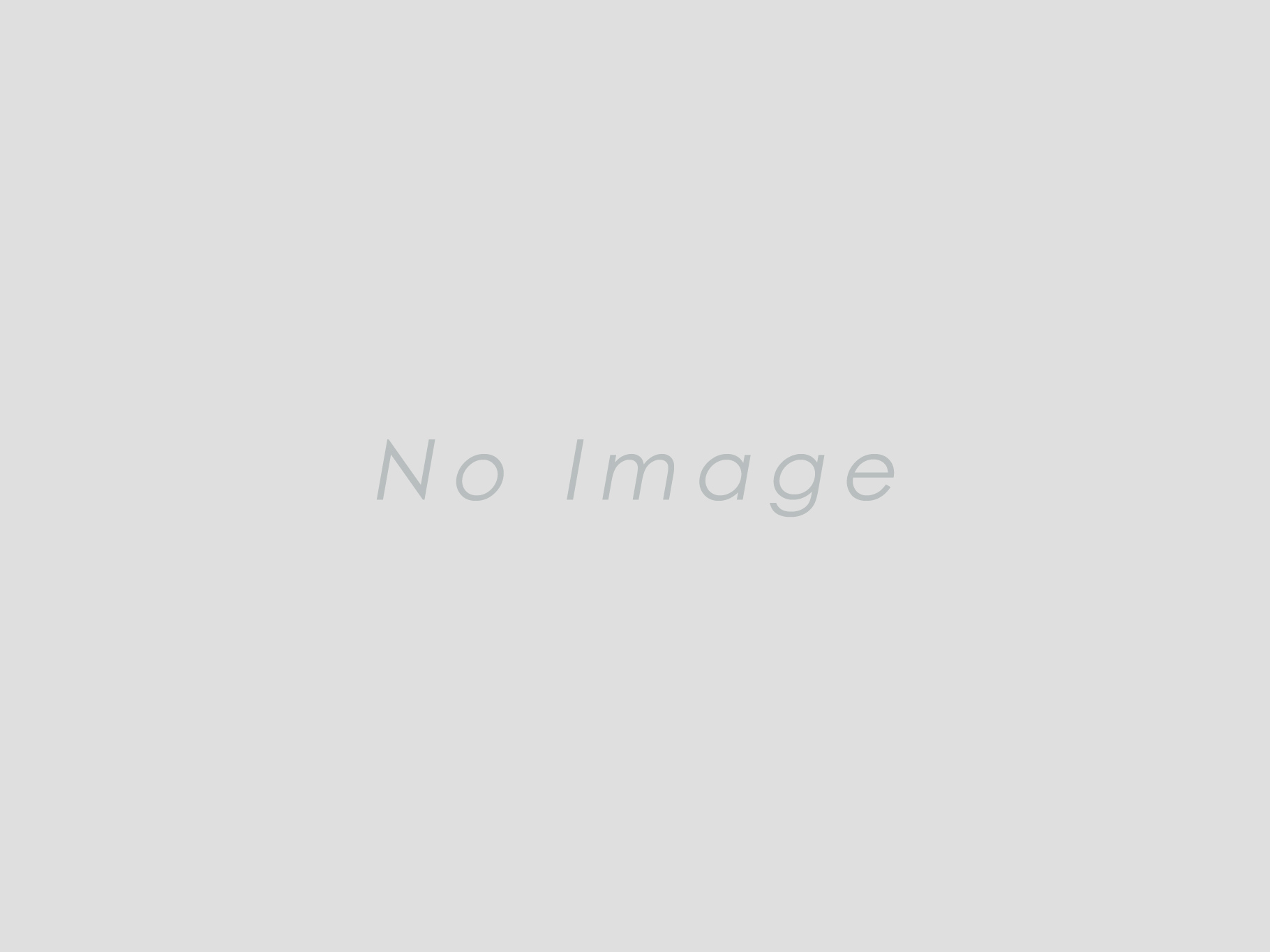
最新レーザー機器の紹介
現在、市場には様々なレーザー軸芯出し機器が存在しています。その中でも特に注目されているのが、ミクロン単位の精度を誇る最新のレーザーアライメントシステムです。この機器は、従来の手動調整に比べて大幅に作業時間を短縮し、より高精度な調整を可能にします。さらに、最新のレーザー機器は複雑な設定を必要とせず、直感的な操作が可能です。これにより、専門知識がない作業者でも高品質な軸芯出しを簡単に行うことができます。また、リアルタイムでデータを解析し、即時にフィードバックを提供するため、機械のダウンタイムを最小限に抑えることができます。
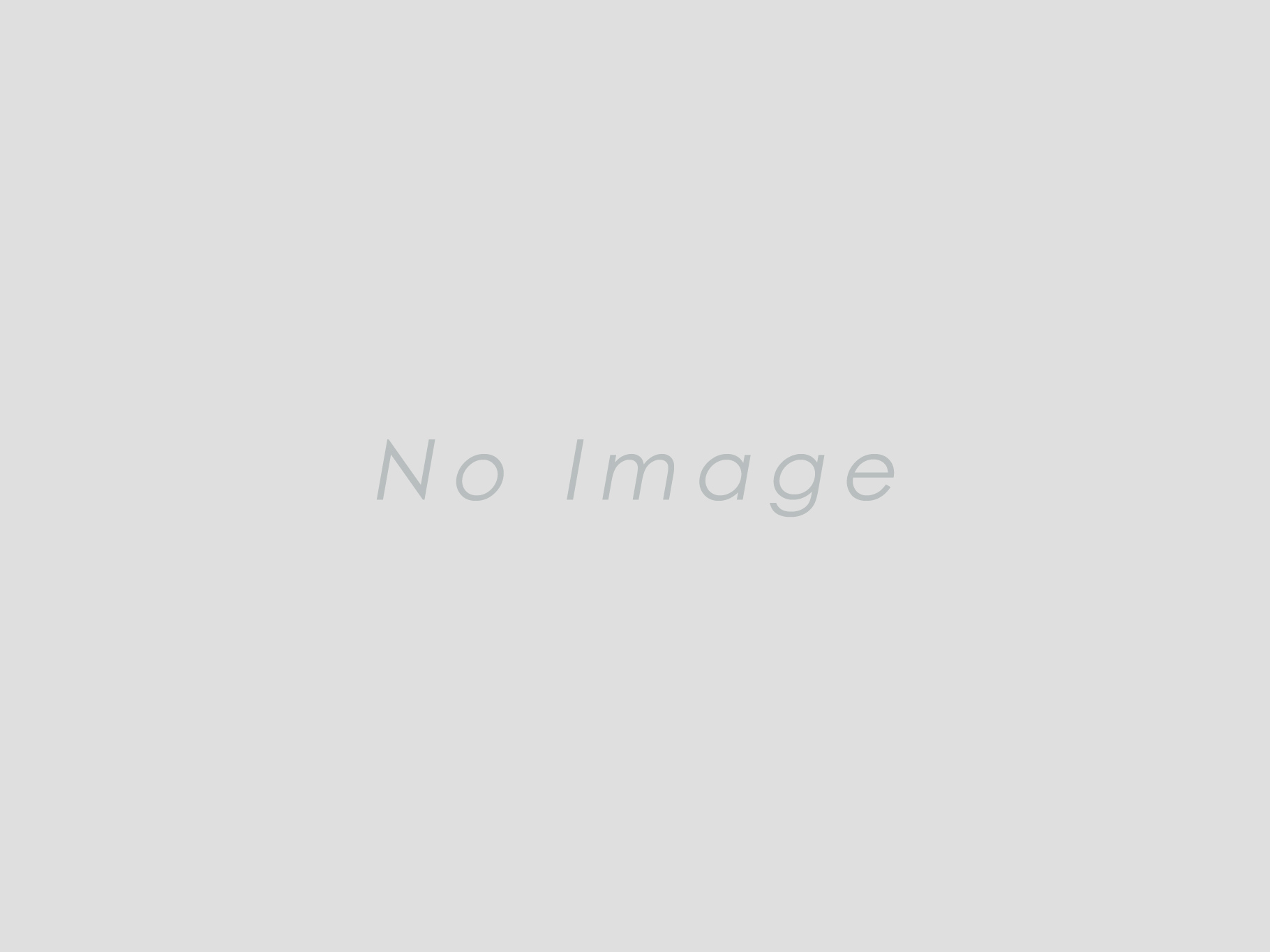
実際の作業現場でのレーザー技術の効果
実際の作業現場でレーザー軸芯出し技術を導入した結果、機械の安定性が大幅に向上しました。特にポンプやモーターの振動が減少し、異常摩耗の防止に繋がっています。レーザー技術による軸芯出しは、従来の方法では検出できなかった微細なズレを瞬時に補正することが可能です。この結果、機械の寿命が延びるだけでなく、エネルギー効率も向上します。例えば、ある製造工場では、レーザー技術を導入することで年間のエネルギーコストを大幅に削減することができました。さらに、作業者の負担も軽減され、安全性も向上しています。これにより、全体的な生産性が向上し、競争力が強化されるという効果が得られています。
ミクロン単位の精度を実現するレーザーによる軸芯出し方法
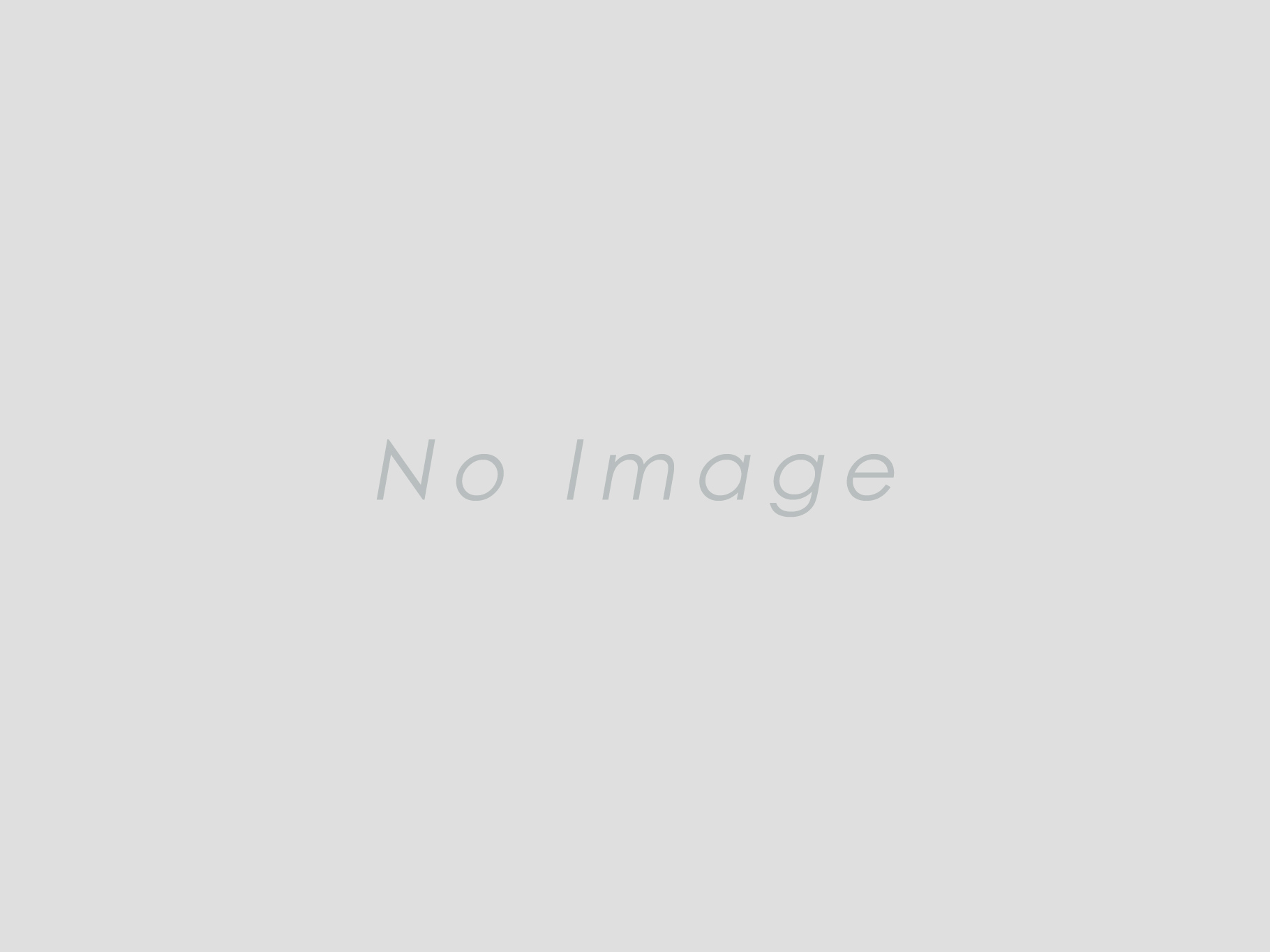
ミクロン単位の精度とは
レーザーによる軸芯出し方法は、その精度がミクロン単位にまで達することで知られています。従来の手法では、目視や機械的な測定器具を使用するため、わずかなズレが発生しがちでした。しかし、レーザー技術では光の直進性を利用し、微細なズレも正確に検出可能です。これにより、機械の軸芯をミクロン単位で調整することができ、摩耗やエネルギーロスを大幅に低減します。また、ミクロン単位の精度が実現することで、機械の振動も抑えられ、全体のパフォーマンスが向上します。精度の向上は、機械の寿命延長にも寄与し、長期的なコスト削減にもつながります。
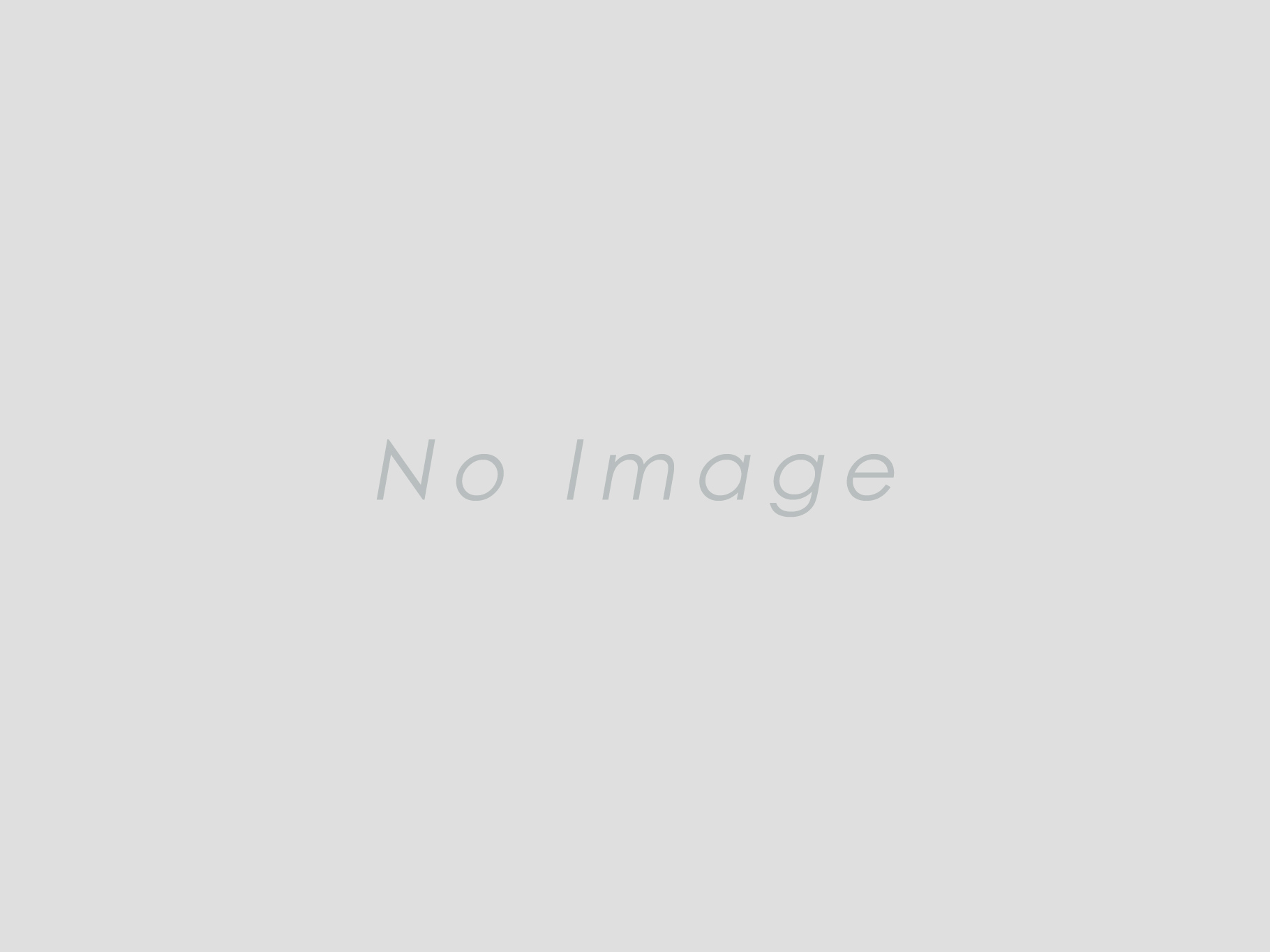
レーザーによる径方向の精密調整
レーザーを使用した径方向の精密調整は、軸芯出し方法の中でも特に効果的です。従来の方法では、調整が手間取り、時間がかかる上に、精度も十分でないことが多々ありました。しかし、レーザー技術はその光の直進性を活かし、迅速かつ正確に径方向のズレを検出し修正することができます。このプロセスでは、レーザー光を機械の軸に照射し、反射光の角度や位置を分析することで、微小なズレを特定します。その後、適切な調整を行うことで、ミクロン単位の精度で軸芯を合わせることが可能となります。このようにして、レーザーによる径方向の精密調整は、作業効率と機械のパフォーマンスを飛躍的に向上させるのです。
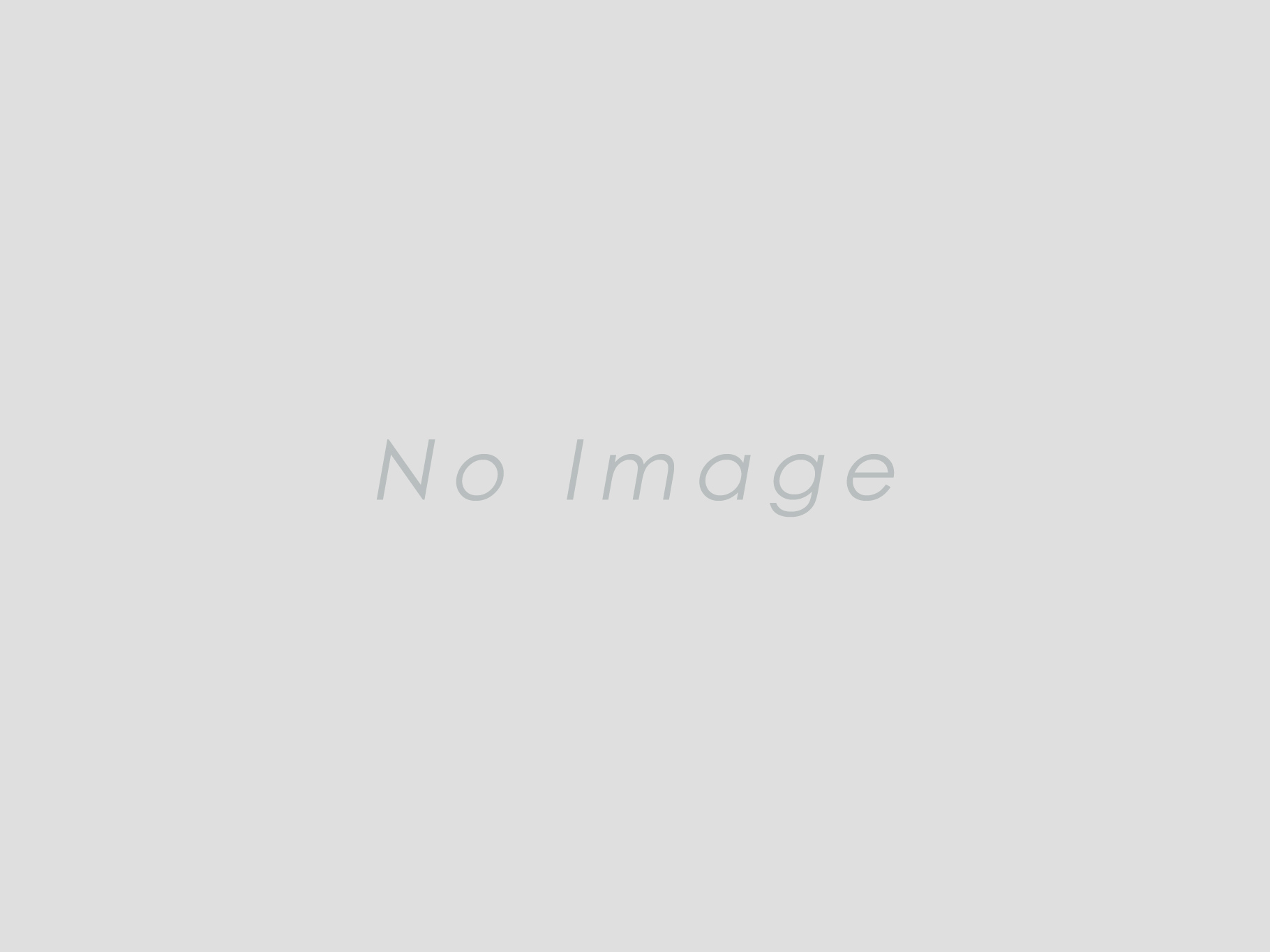
軸芯出し作業のステップバイステップガイド
レーザーによる軸芯出し方法のステップバイステップガイドを紹介します。まず、作業を開始する前に、レーザー軸芯出し器の電源を入れ、適切な位置に設置します。次に、目標とする軸芯の位置にレーザーを照射し、画面に表示されるガイドに従って微調整を行います。この段階では、レーザーの角度や強度を調整することで、精度の高い軸芯出しが可能となります。微調整が完了したら、軸芯位置を再度確認し、誤差がないかチェックします。この一連のステップを踏むことで、ミクロン単位の精度で軸芯出しを行うことができ、機械の性能を最大限に引き出すことができます。
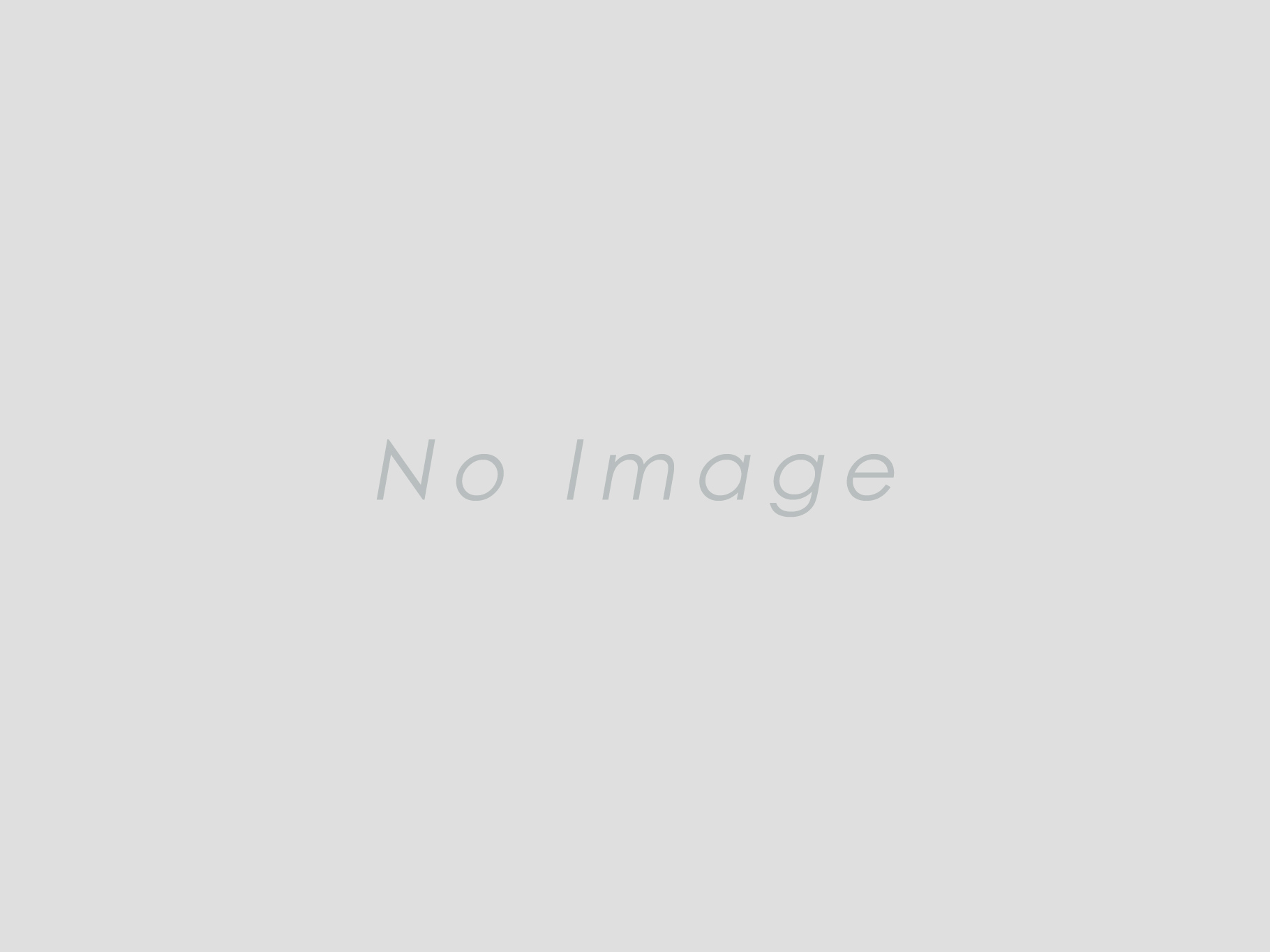
精度を保つためのレーザー機器の校正
精度の高い軸芯出しを維持するためには、レーザー機器の定期的な校正が不可欠です。まず、校正のタイミングについてですが、通常は使用頻度や作業環境に応じて、定期的に行うことが推奨されます。具体的な校正方法としては、基準となる軸芯を用いてレーザーの出力や角度を調整し、精度を確認します。この際、微小な誤差も見逃さないようにしっかりとチェックすることが重要です。また、校正作業は専門知識が必要なため、技術者による実施が望ましいです。定期的な校正を行うことで、常に高精度な軸芯出しが可能となり、機械の長寿命化や効率的な運用に寄与します。
効率的な軸芯出しを可能にするレーザー技術の利点
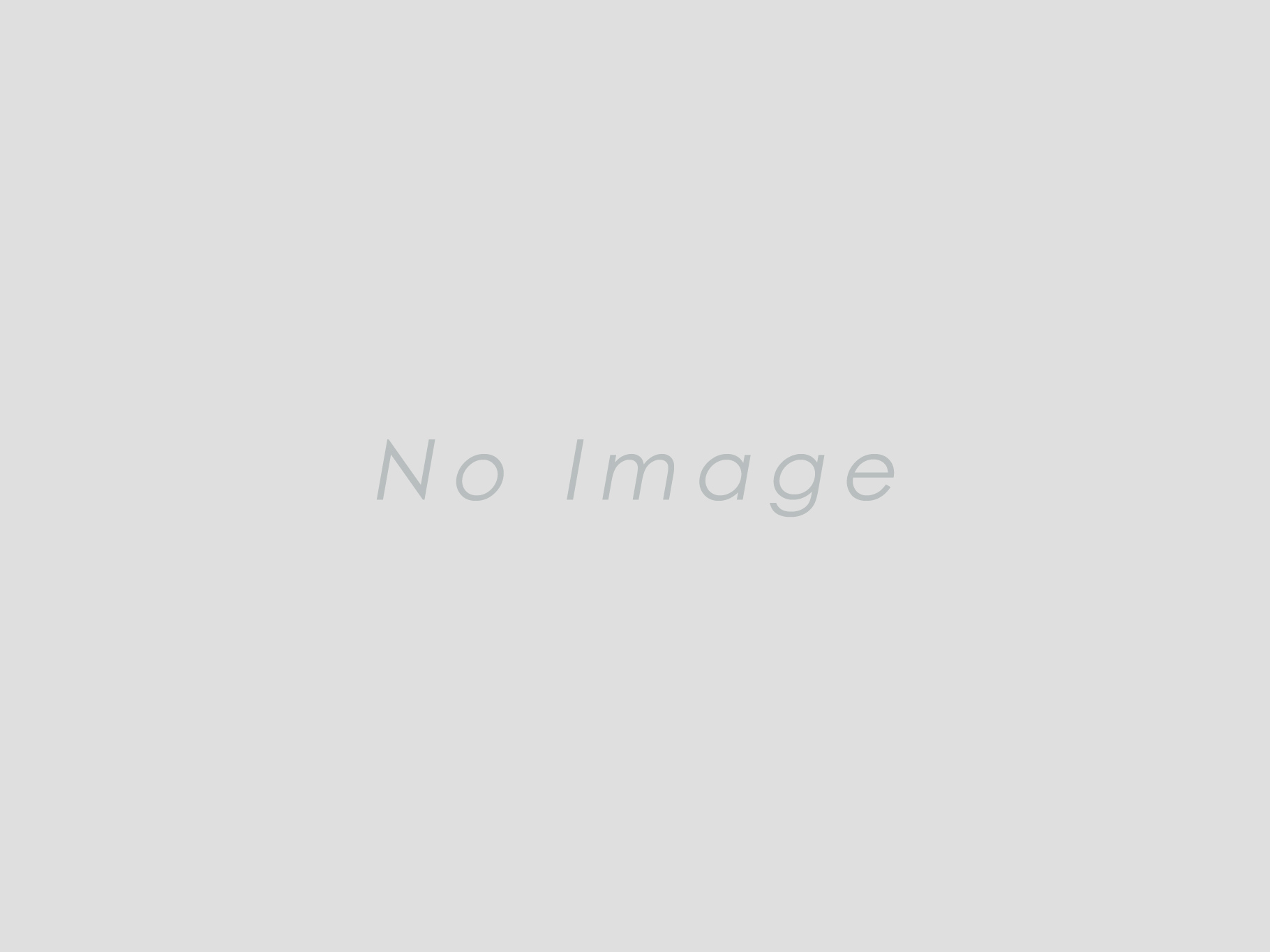
作業時間の短縮と効率化
レーザーを用いた軸芯出し方法は、従来の手法に比べて作業時間を大幅に短縮することができます。従来の手法では、機械の軸芯を正確に合わせるために多くの時間が必要でしたが、レーザー技術を活用することでこの作業が迅速に行えるようになりました。例えば、以前は数時間かかっていた軸芯調整が、レーザーによって数十分で完了することが可能です。これにより、生産ラインの停止時間が大幅に短縮され、全体の生産効率が向上します。さらに、作業者の負担も軽減されるため、長時間の作業による疲労を防ぐことができます。
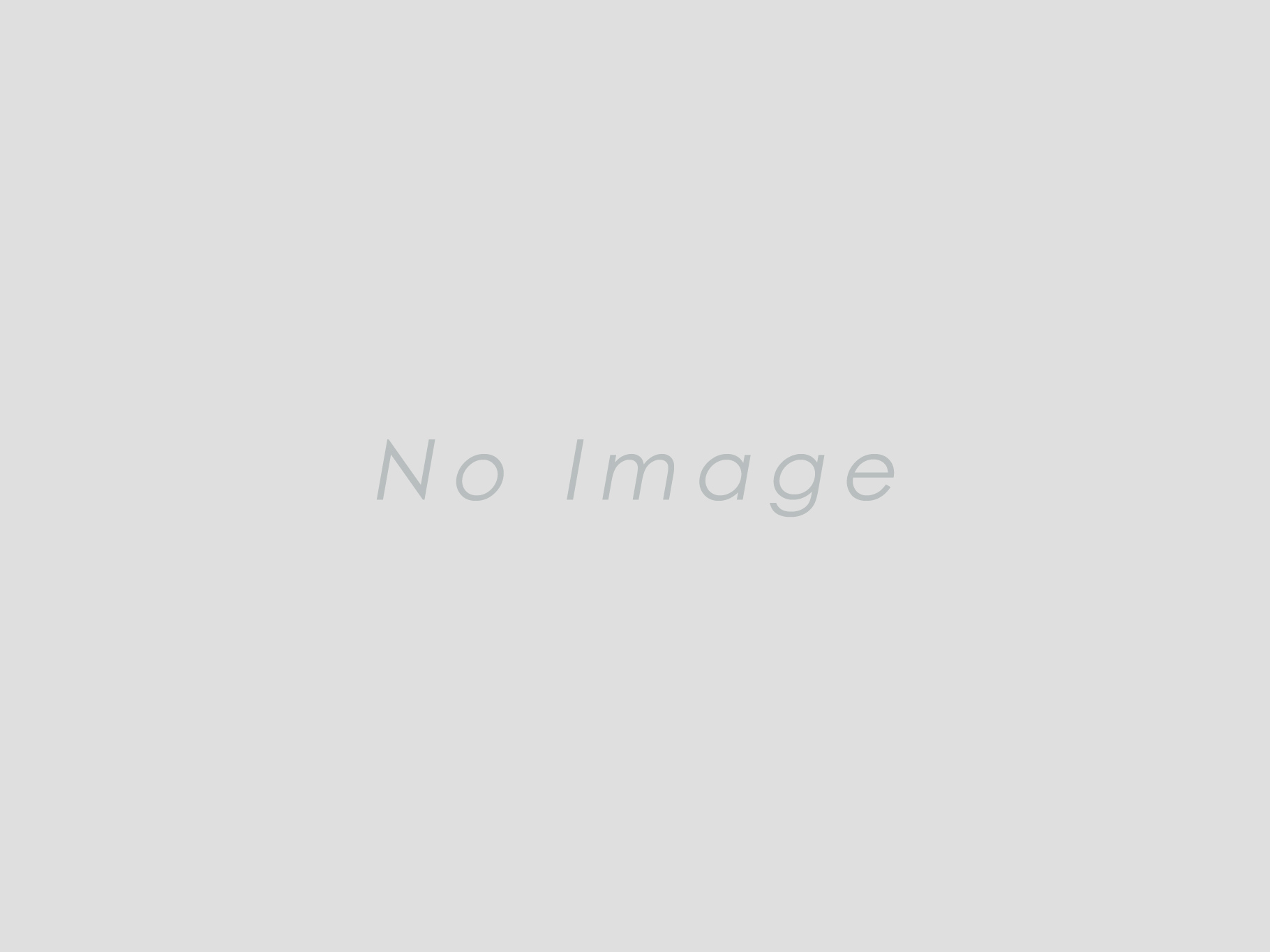
高精度と低コストの両立
レーザーによる軸芯出し方法は、ミクロン単位の高精度を実現するため、機械のパフォーマンスを最適化します。この高精度なアライメント調整により、機械の摩耗やエネルギーロスが最小限に抑えられ、長期的にはメンテナンスコストを削減することができます。さらに、初期投資が高いとされるレーザー機器も、長期間にわたって使用することでトータルコストの低減が可能です。高精度と低コストの両立は、企業が競争力を維持し、効率的な運用を実現するための鍵となります。これにより、レーザーを用いた軸芯出し方法は、経済的なメリットと技術的な優位性を同時に享受することができます。
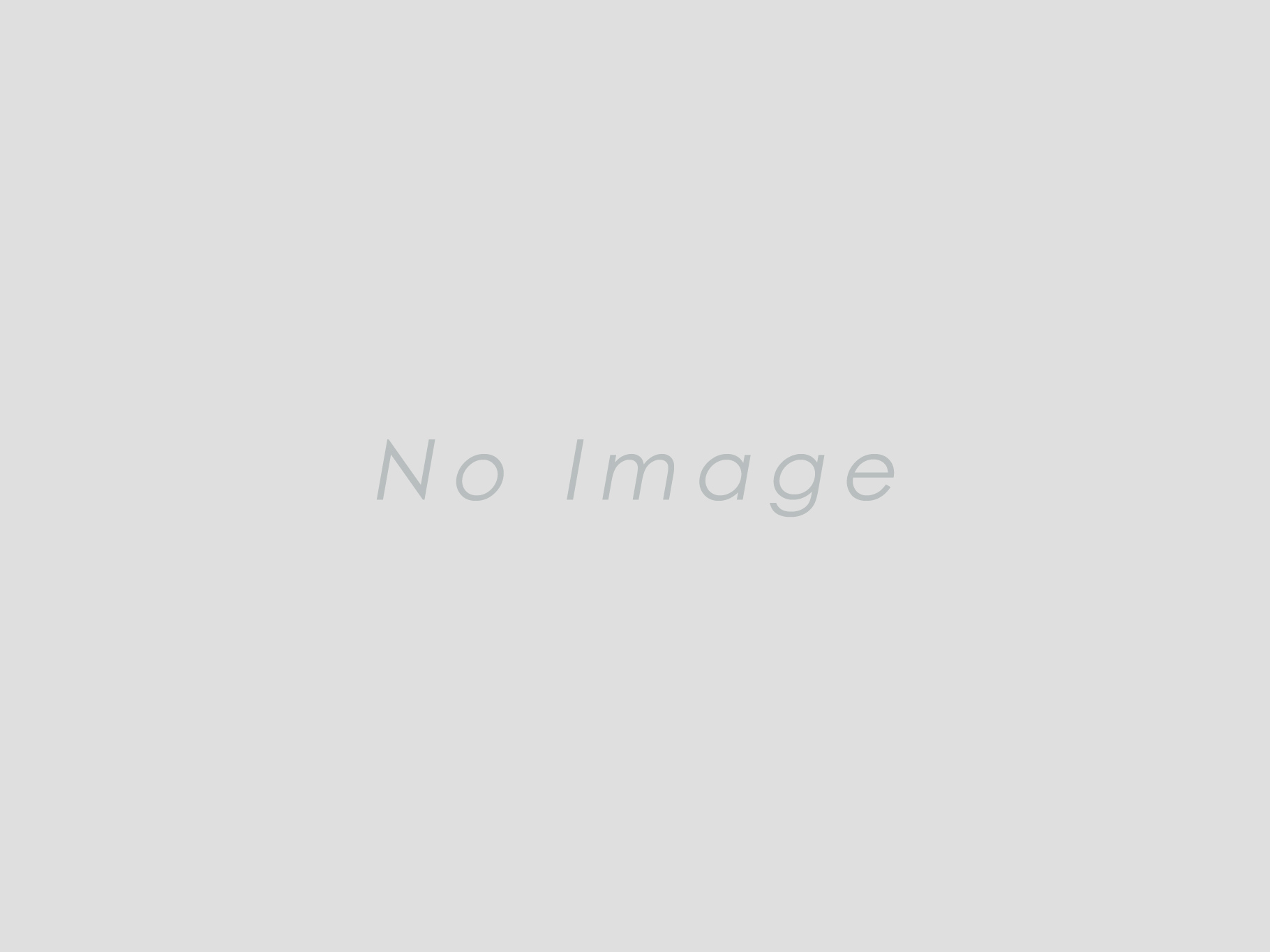
レーザー技術の導入による生産性向上
レーザー技術の進化により、軸芯出し方法が劇的に効率化されました。従来の手動調整では、数時間から数日を要することもありましたが、レーザーを用いることで、僅か数分で高精度な軸芯調整が可能となりました。この技術の導入により、機械の稼働時間が最大化され、生産ライン全体の生産性が急上昇します。また、摩擦やエネルギーロスが最小限に抑えられるため、長期的な運用コストの削減にも繋がります。これにより、企業はより効率的かつ持続可能な運用を実現できます。
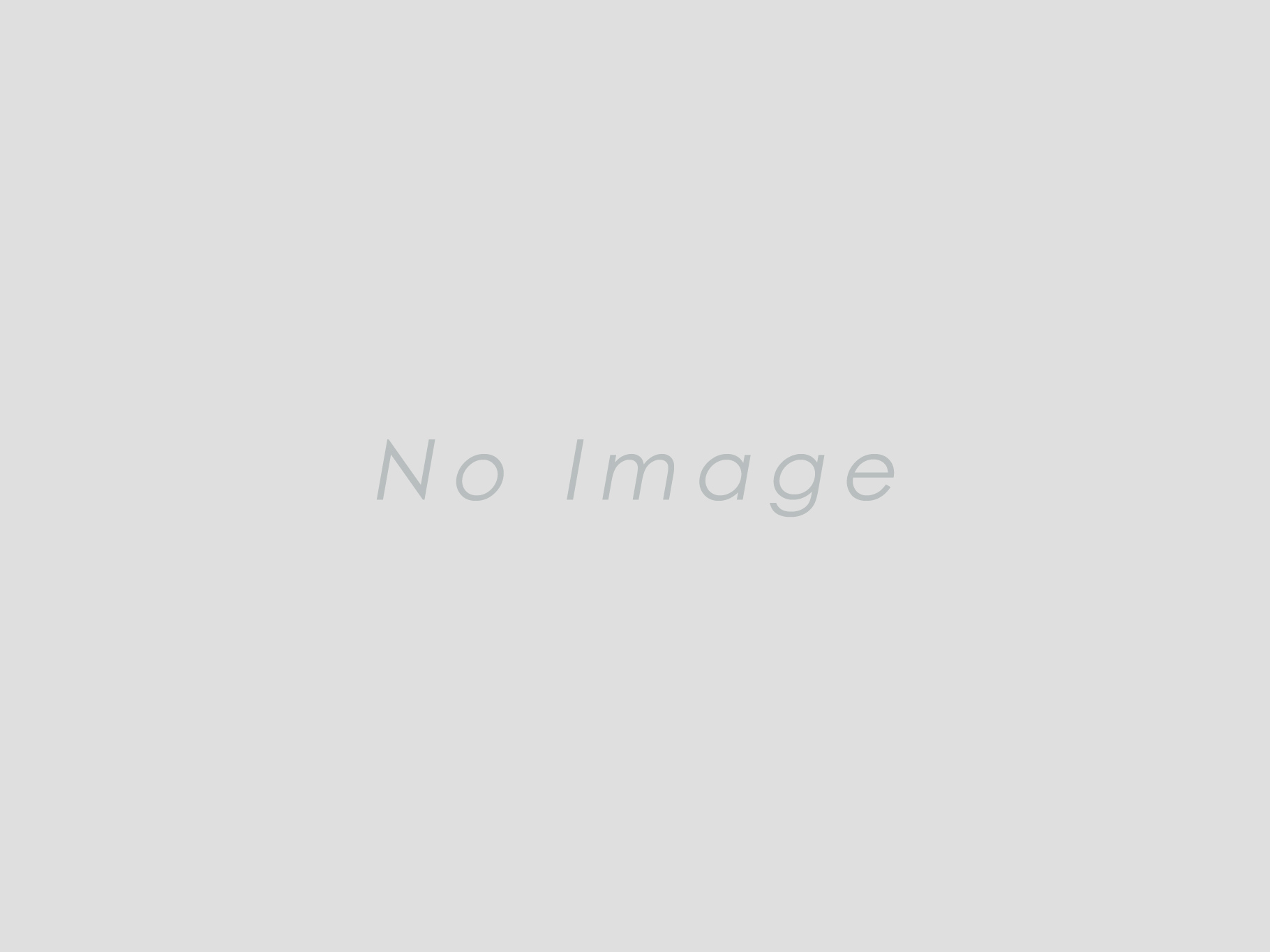
操作の簡便さと安全性
レーザーを用いた軸芯出し方法は、操作の簡便さと安全性も非常に高いです。従来の方法では高度な技能が求められましたが、レーザー技術の導入により、どなたでも短時間で習得可能です。操作手順がシンプルで、直感的に理解できるため、試行錯誤の時間を大幅に短縮できます。また、レーザーを使用することで、機械に触れることなく非接触で作業が行えるため、作業者の安全性も確保されます。これにより、作業の効率向上と事故のリスク軽減が同時に達成されます。
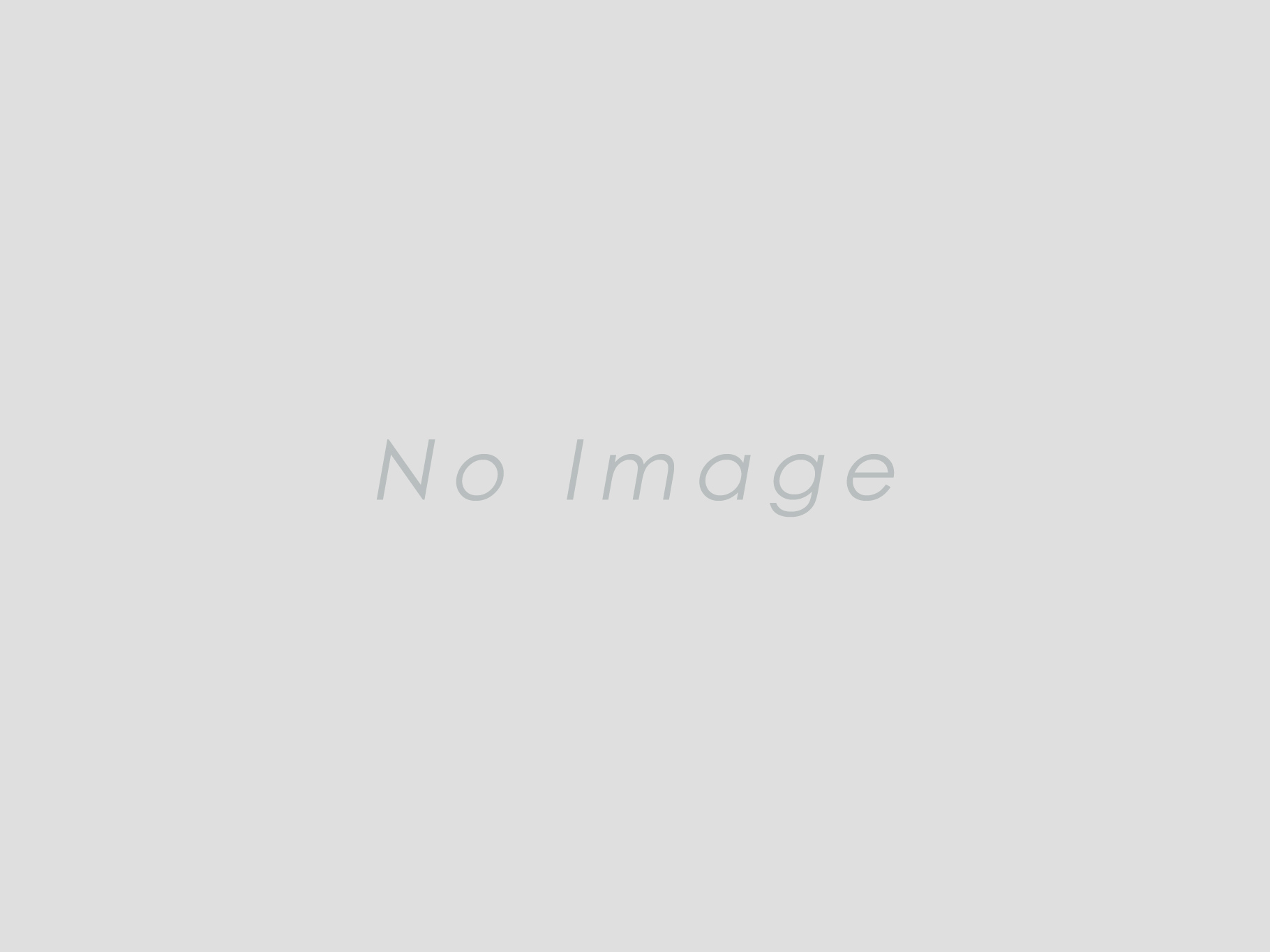
従来技術とのトータルコストの比較
従来の軸芯出し方法とレーザー技術を用いた方法を比較すると、トータルコストの観点からも多くの利点が見えてきます。従来の手法では、作業時間が長く、複数の工程を経ることが多いため、人件費や機械の停止時間が増加します。一方、レーザー軸芯出し技術は、作業時間の短縮と高精度な調整が可能で、その結果、直接的なコストも大幅に削減されます。さらに、精度の高いレーザー技術を使用することで、機械の摩耗や故障が減少し、長期的なメンテナンスコストも削減されます。このようなトータルコストの低減効果は、企業にとって大きなメリットと言えるでしょう。
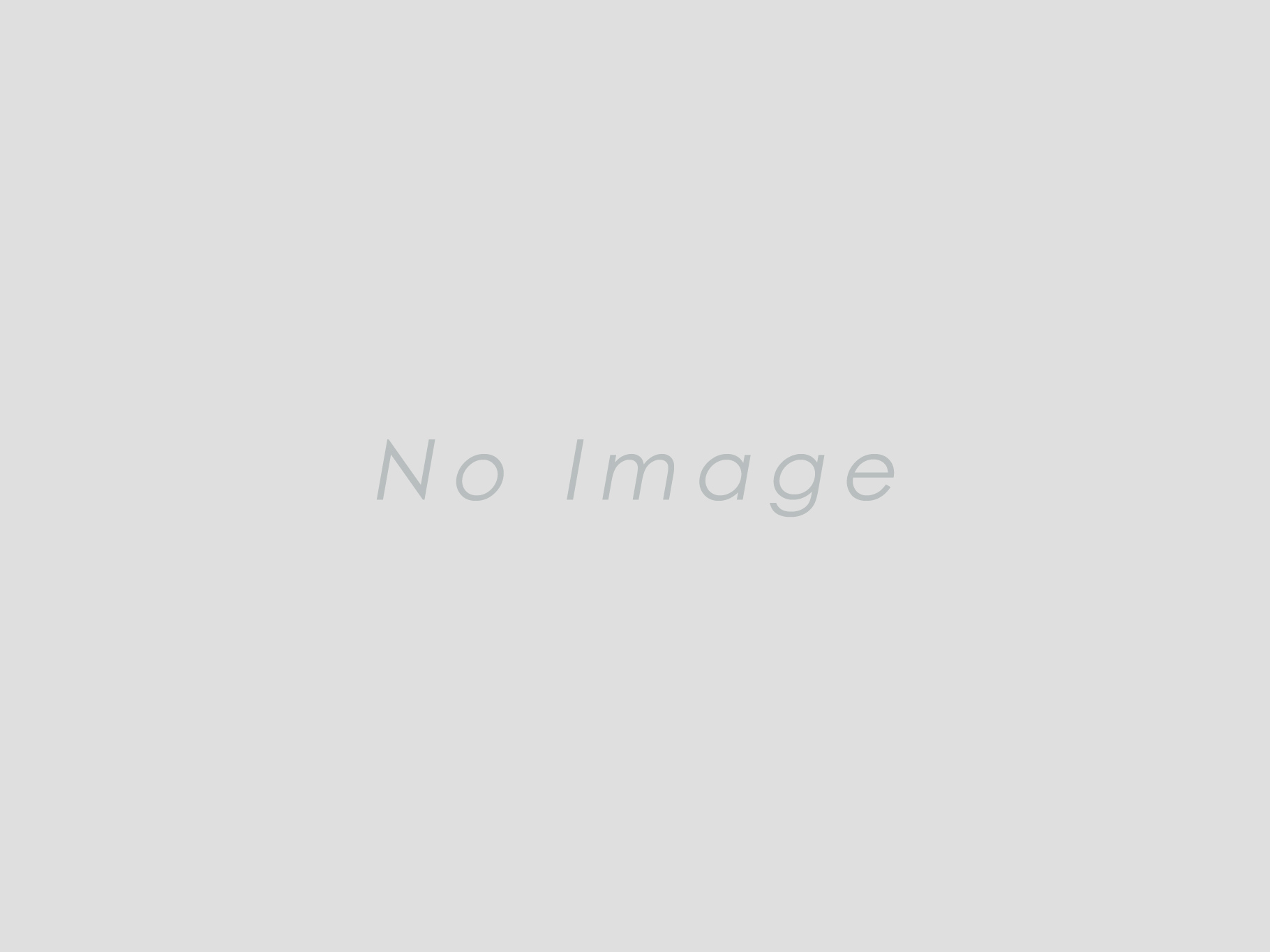
レーザー技術によるメンテナンスの効率化
レーザー技術を導入することで、メンテナンス作業が飛躍的に効率化されます。従来の軸芯出し方法では、技術者が手作業で調整を行うため、時間がかかり、精度にも限界がありました。しかし、レーザー技術を用いることで、ミクロン単位の高精度な調整が迅速に行えるようになり、作業時間が大幅に短縮されます。また、レーザー軸芯出し器の操作は簡便で、安全性も高いため、技術者の負担が軽減されるとともに、作業の品質も向上します。これにより、機械の稼働率が向上し、機械停止による生産ロスを最小限に抑えることができます。レーザー技術の導入により、メンテナンスの効率化とコスト削減が同時に実現できるのです。
レーザー軸芯出し方法で摩擦とエネルギーロスを最小化
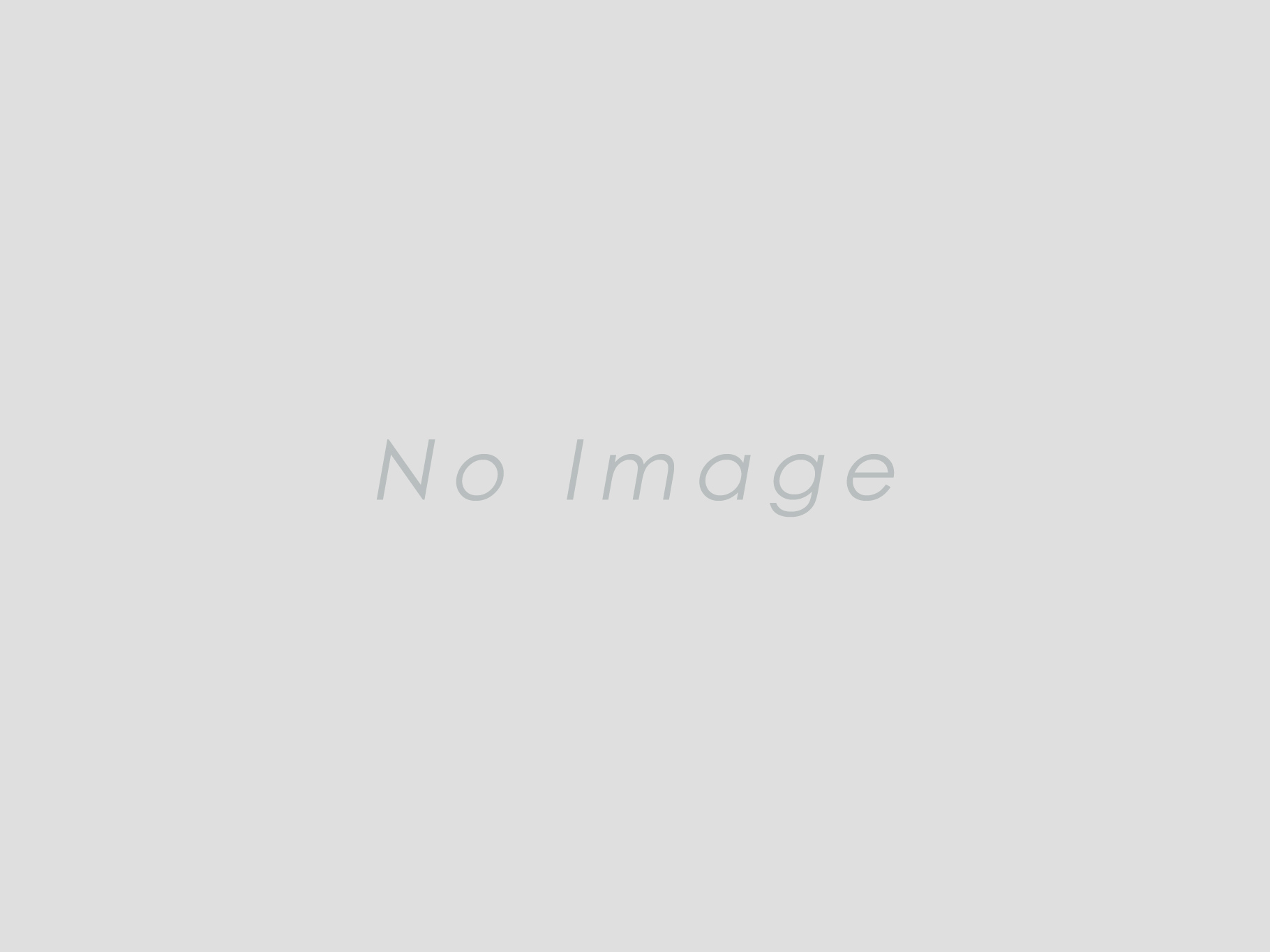
摩擦の低減と機械寿命の延長
レーザーによる軸芯出し方法は、産業機械の摩擦を劇的に低減する効果があります。従来の手法では、微細なズレが摩擦を引き起こし、機械の寿命を短くする要因となっていました。しかし、レーザー技術を用いることで、ミクロン単位の精度で軸芯を調整することが可能となり、摩耗や故障のリスクを大幅に減少させます。これにより、機械の寿命が延長され、メンテナンスや部品交換にかかるコストも削減されるのです。さらに、摩擦が減少することで、エネルギー効率も向上し、運用コストの面でも大きなメリットがあります。レーザー軸芯出し方法は、産業機械の持続可能な運用を支える重要な技術として注目されています。
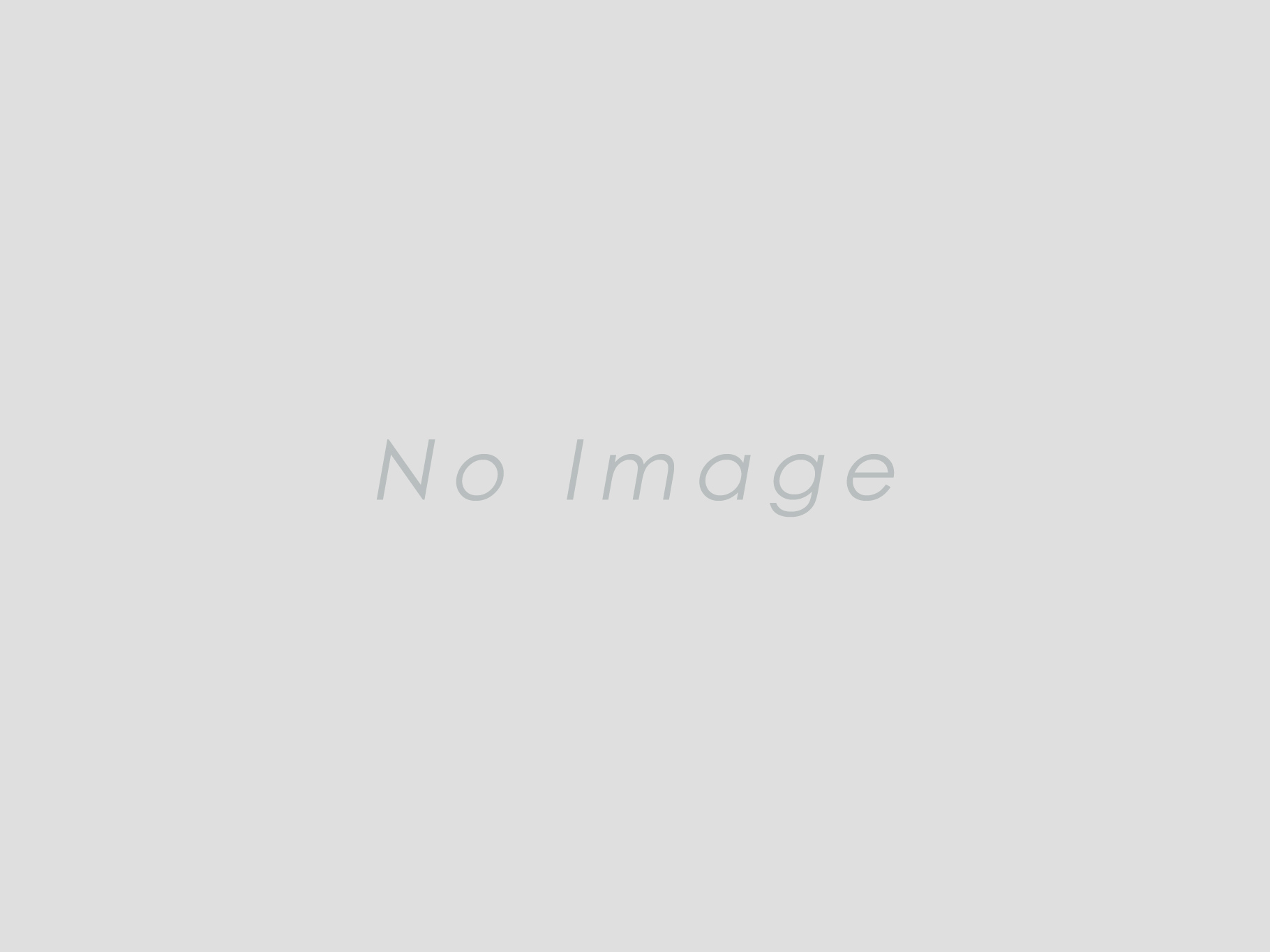
エネルギーロス削減の原理
レーザーによる軸芯出し方法は、エネルギーロス削減にも大きな効果を発揮します。軸芯が正確に合っていない状態では、機械の回転運動に無駄なエネルギーが消費されます。これが摩擦や振動として現れ、結果的にエネルギーロスを引き起こします。しかし、レーザー技術を用いて軸芯を精密に調整することで、こうした無駄なエネルギー消費を最小限に抑えることができます。エネルギーロスが減少することで、運用コストの削減はもちろん、環境負荷の低減にもつながります。特に、大規模な工場やプラントにおいては、その効果は顕著であり、持続可能なエネルギー管理に貢献します。レーザー軸芯出し方法は、エネルギー効率の向上とコスト削減を両立するための有効な手段といえるでしょう。
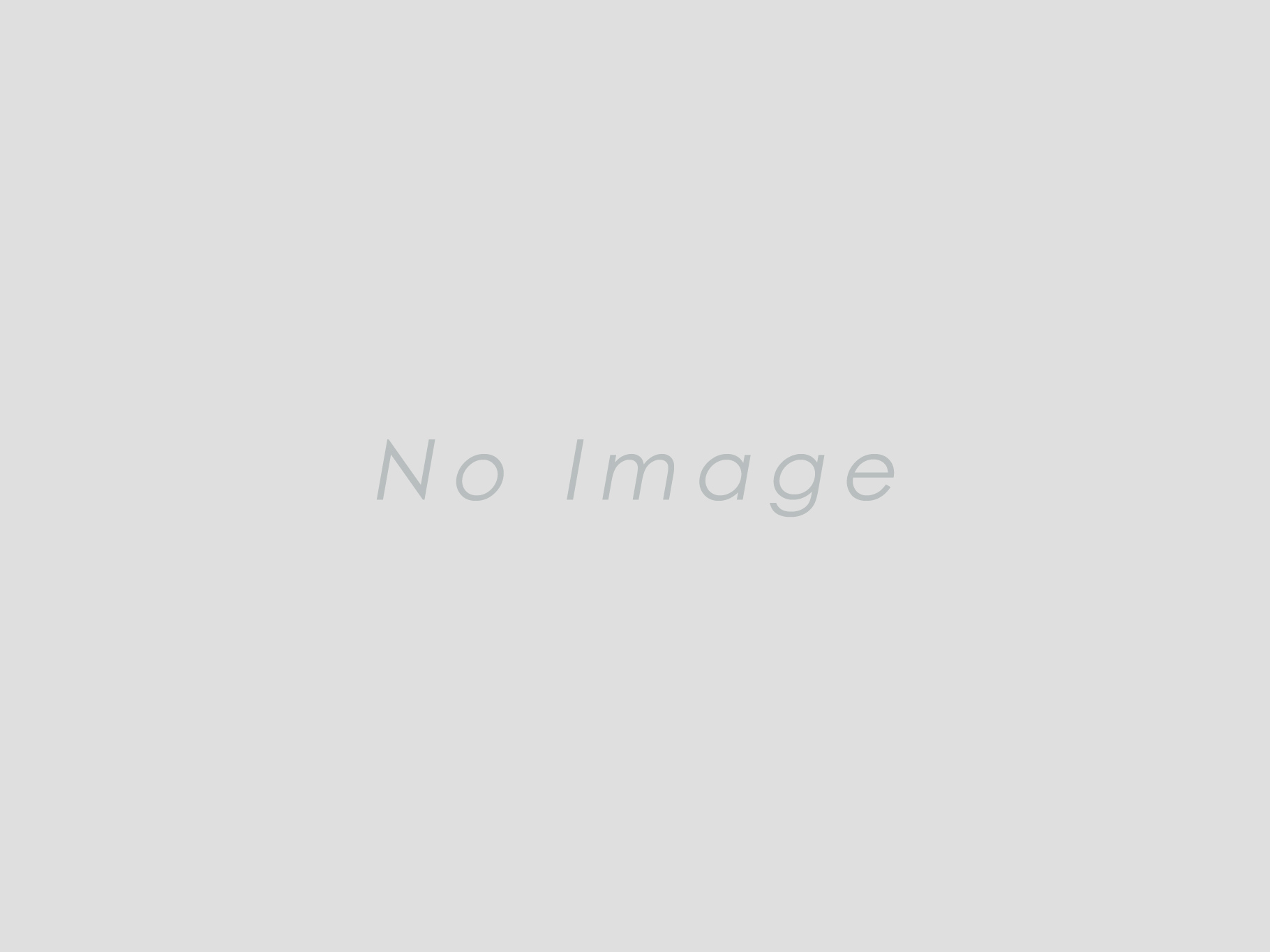
レーザー軸芯出しの具体的な方法
レーザー軸芯出し方法は、精度と効率を高めるための最先端技術として注目されています。まず、レーザー軸芯出し器を使用する前に、機械の初期状態を確認し、全体のアライメントが必要かどうかを判断します。次に、レーザー軸芯出し器を設置し、レーザービームを発射します。このビームは非常に直線的で正確であり、微小な軸のズレも検出することができます。そして、受光部分にビームが当たった位置を基に、コンピュータソフトウェアで自動的にズレを計算し、補正のための具体的な数値を提供します。最後に、その数値を基に手動または自動で調整を行い、正確な軸芯出しを完了します。このプロセスは、従来の手動での確認作業と比べて時間の短縮と精度の向上を同時に実現します。
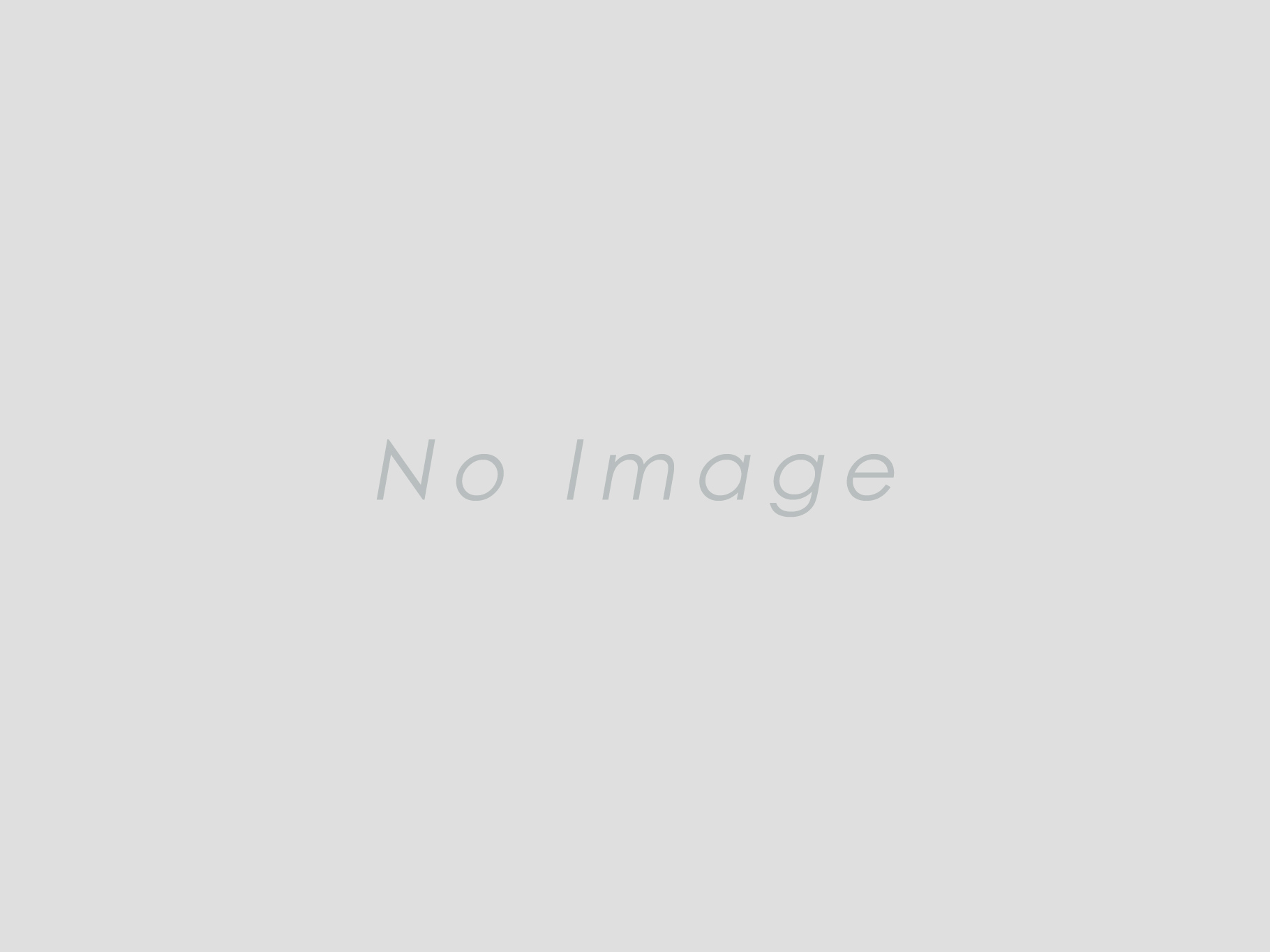
摩擦低減とエネルギー効率の関係
軸芯出し方法には、摩擦低減とエネルギー効率向上の重要な関連性があります。適切に軸芯出しされた機械は、摩擦が最小限に抑えられ、エネルギーロスも減少します。これは、摩擦が少ないほど機械の部品がスムーズに動作し、エネルギーの消費量も減少するためです。特にレーザーを用いた軸芯出し方法では、ミクロン単位の高精度な調整が可能であり、微細なズレも修正できます。この高精度な調整により、摩擦による異常摩耗やエネルギーロスが発生しにくくなります。結果として、機械の寿命が延び、運用コストの削減にも繋がります。また、エネルギー効率が向上することで、持続可能な生産体制の構築にも寄与します。このように、レーザー軸芯出しは単に精度を高めるだけでなく、総合的なエネルギー効率の向上にも大きく貢献するのです。
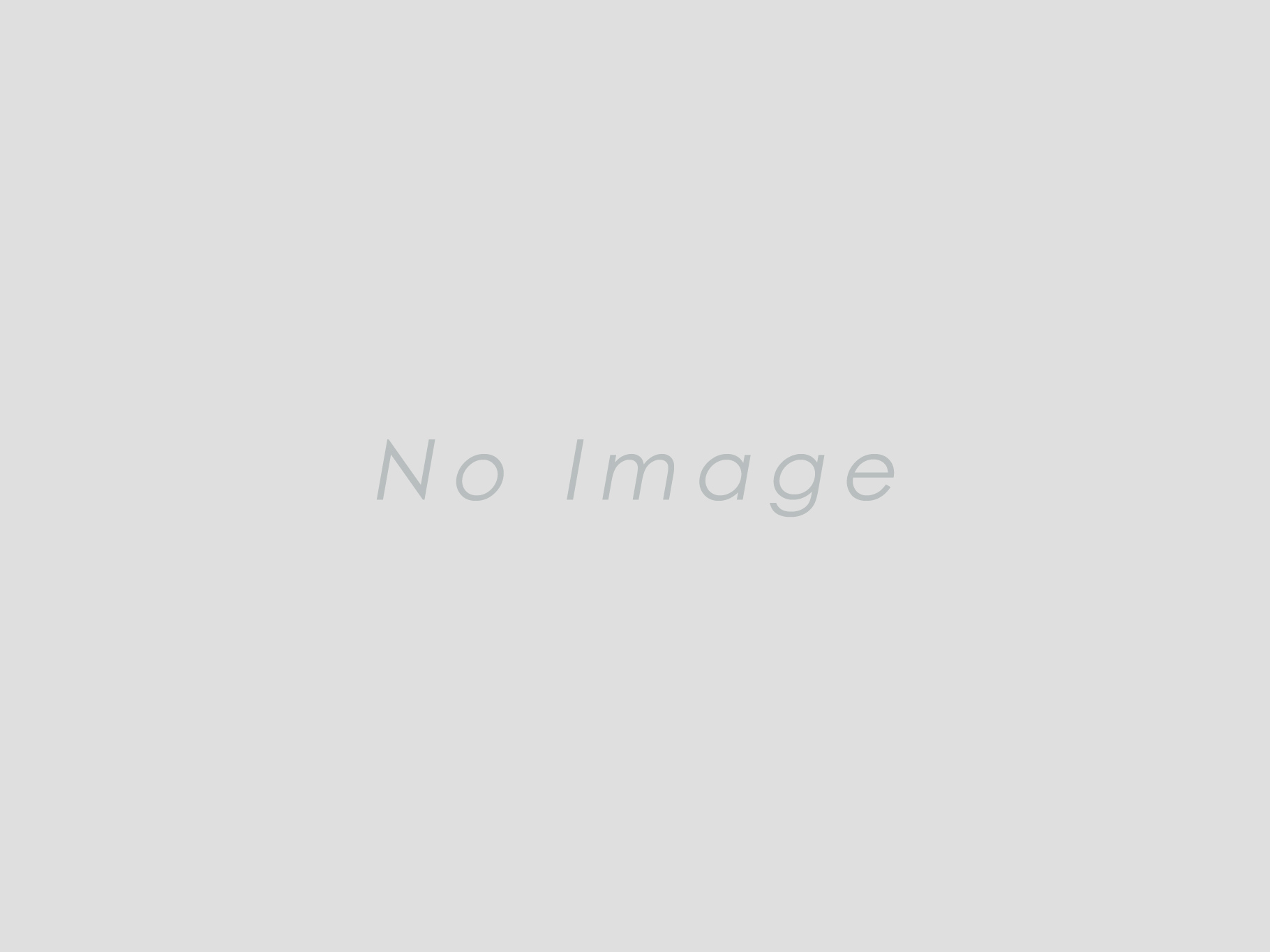
実際のエネルギーコスト削減例
レーザー軸芯出し方法は、多くの工場でエネルギーコストの削減に寄与しています。具体例として、ある製造工場では、レーザーを用いてポンプやモーターの軸芯を正確に合わせることで、エネルギーロスを大幅に削減しました。この結果、摩擦が減少し、機械の効率が向上しました。例えば、エネルギー消費量が15%減少し、運用コストも大幅に削減されています。さらに、定期的なメンテナンスが簡便になり、機械の稼働率も向上しました。このような成功例は、他の工場でも導入を促進し、全体的なエネルギー効率の向上に貢献しています。レーザー軸芯出し方法は、経済的なメリットだけでなく、環境保護にも大いに貢献する技術です。
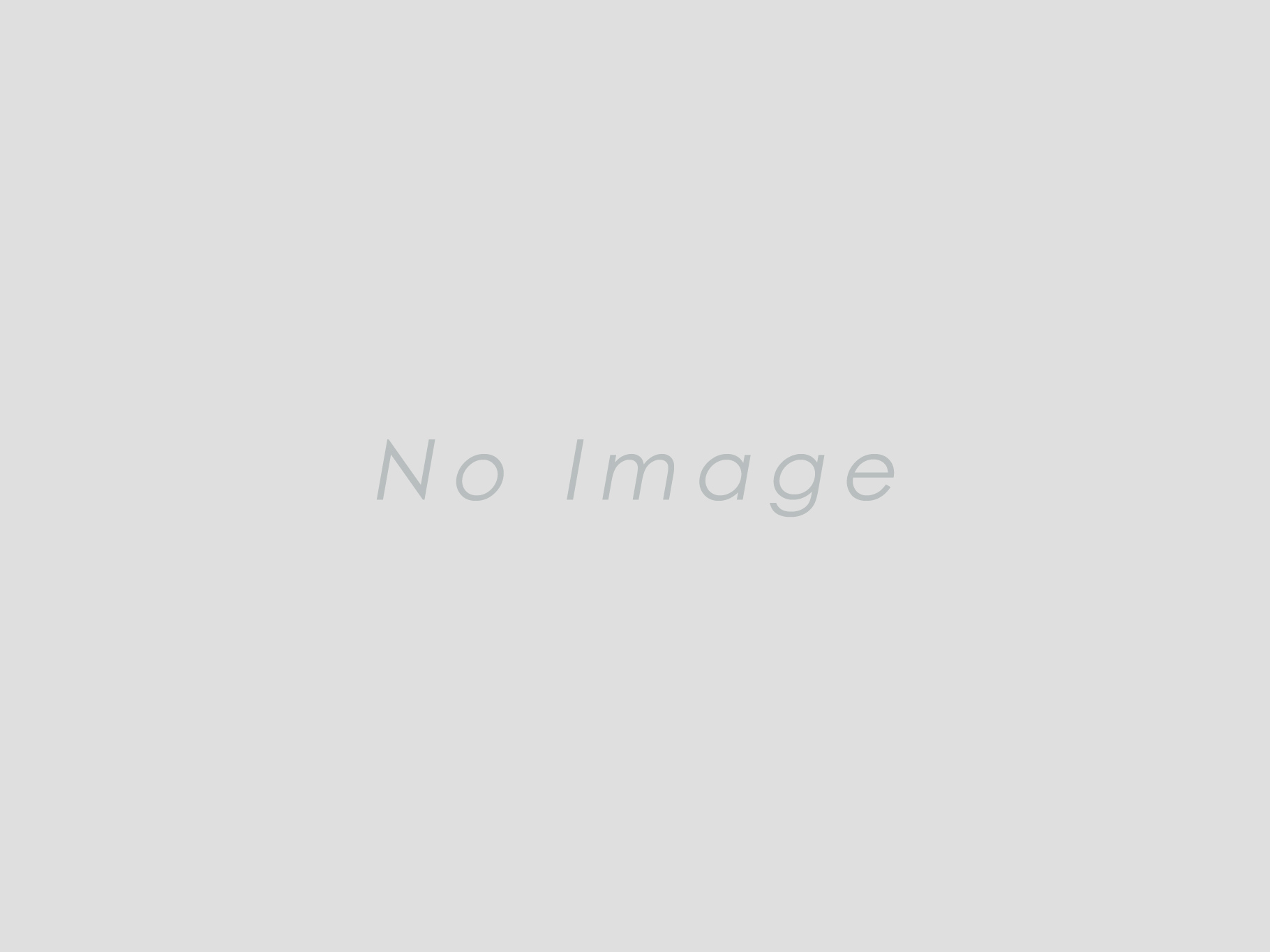
レーザー技術の環境への影響
レーザー軸芯出し方法は、環境への影響も大きく改善します。従来の方法に比べて、エネルギーロスが少なくなるため、CO2排出量の削減にもつながります。例えば、ある工場ではレーザー技術を導入した結果、年間のCO2排出量が約10%削減されました。このように、レーザー軸芯出し方法は持続可能な製造プロセスの一部として非常に有効です。また、精度が高いため、機械の寿命が延び、廃棄物の削減にも寄与しています。この結果、環境負荷が減少し、企業の環境責任の向上にもつながります。レーザー技術の導入は、経済的効果と環境保護の両面で大きなメリットをもたらすため、今後も多くの産業で広く活用されることが期待されます。
産業機械の精度向上:レーザー技術が切り拓く未来
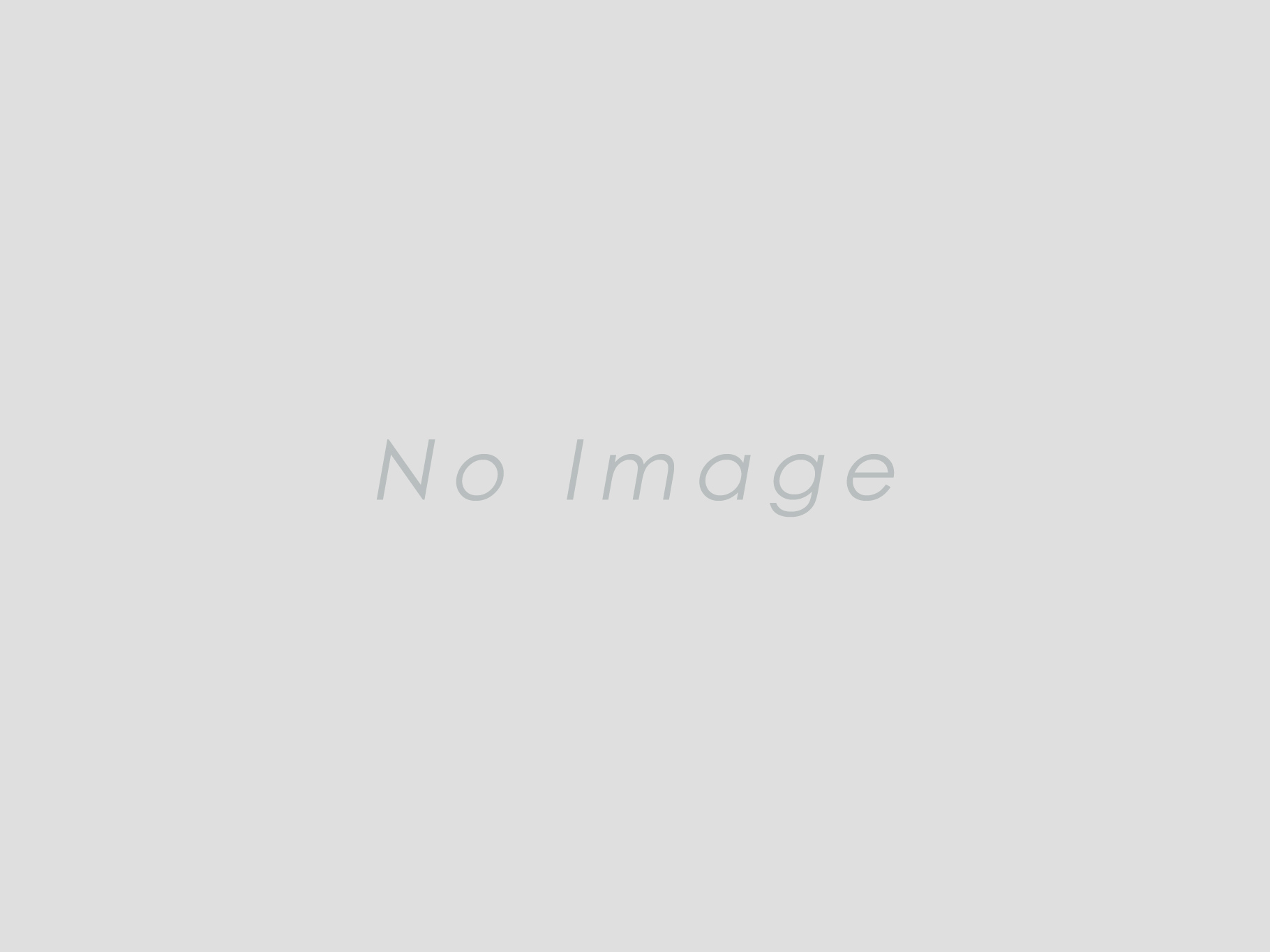
産業機械における精度向上の重要性
産業機械の運用において、精度向上は生産性や効率性を大きく左右する要因です。軸芯出し方法の正確さは、機械の動作に直接影響を与えます。従来の手法では、手作業による調整が主流であり、精度に限界がありました。しかし、レーザー技術を用いた軸芯出し方法により、ミクロン単位での精度が実現可能となりました。これにより、摩擦やエネルギーロスを大幅に低減し、機械の寿命延長やメンテナンスコストの削減にも寄与します。このように、精度向上がもたらすメリットは計り知れません。
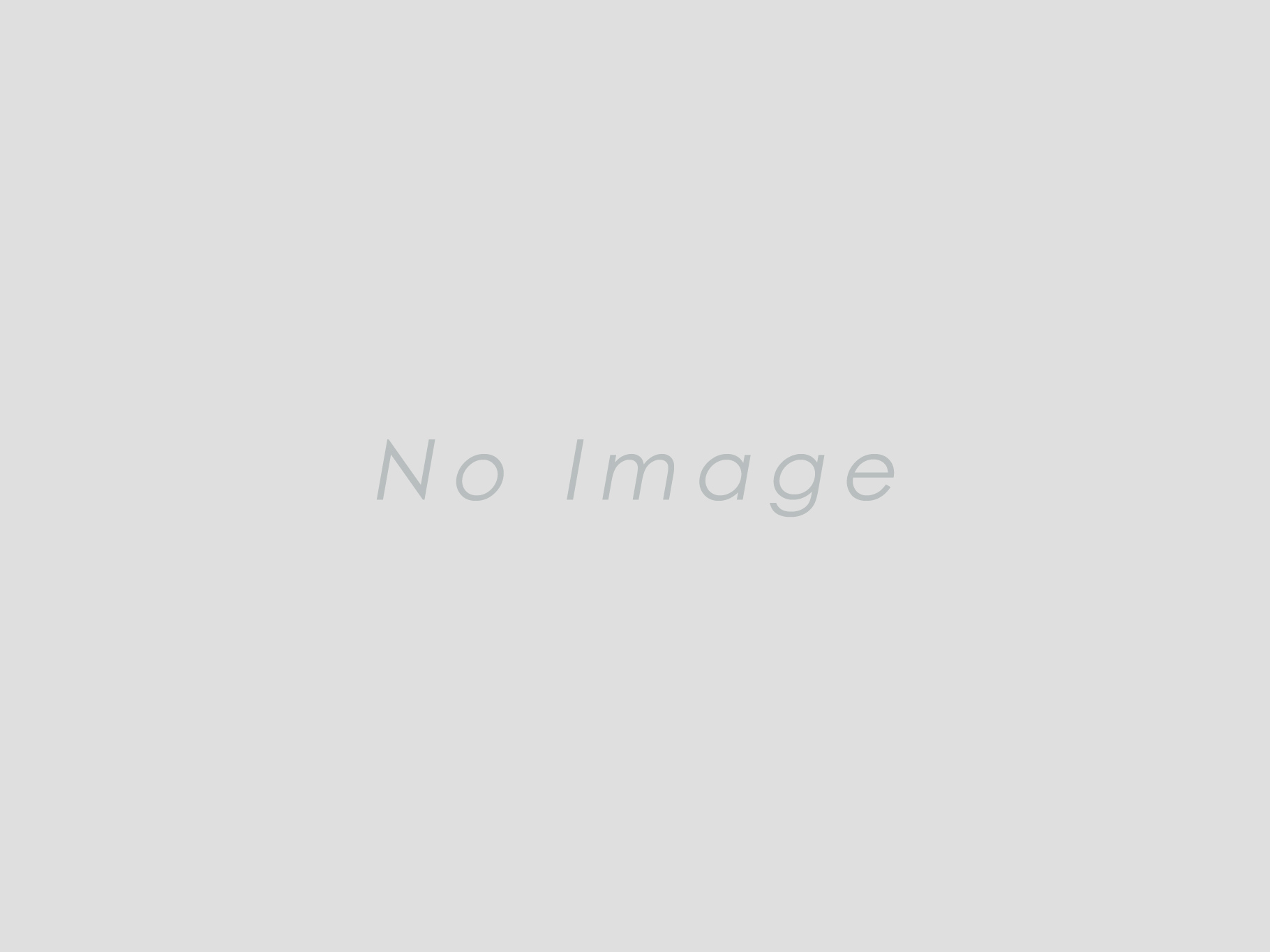
レーザー技術の未来展望
レーザー技術は、今後ますます重要な役割を果たすことが予想されます。特に軸芯出し方法においては、その精度と効率性が評価されています。最新のレーザー機器は、より高速かつ高精度な調整を可能にし、産業界における生産性の向上に大きく貢献しています。また、レーザー技術は他の自動化技術とも融合し、スマート工場の実現に向けた重要な要素となっています。今後の研究開発においても、さらに高性能なレーザー機器が登場することでしょう。これにより、産業機械の精度向上が一層進むとともに、新たな産業革命が期待されます。
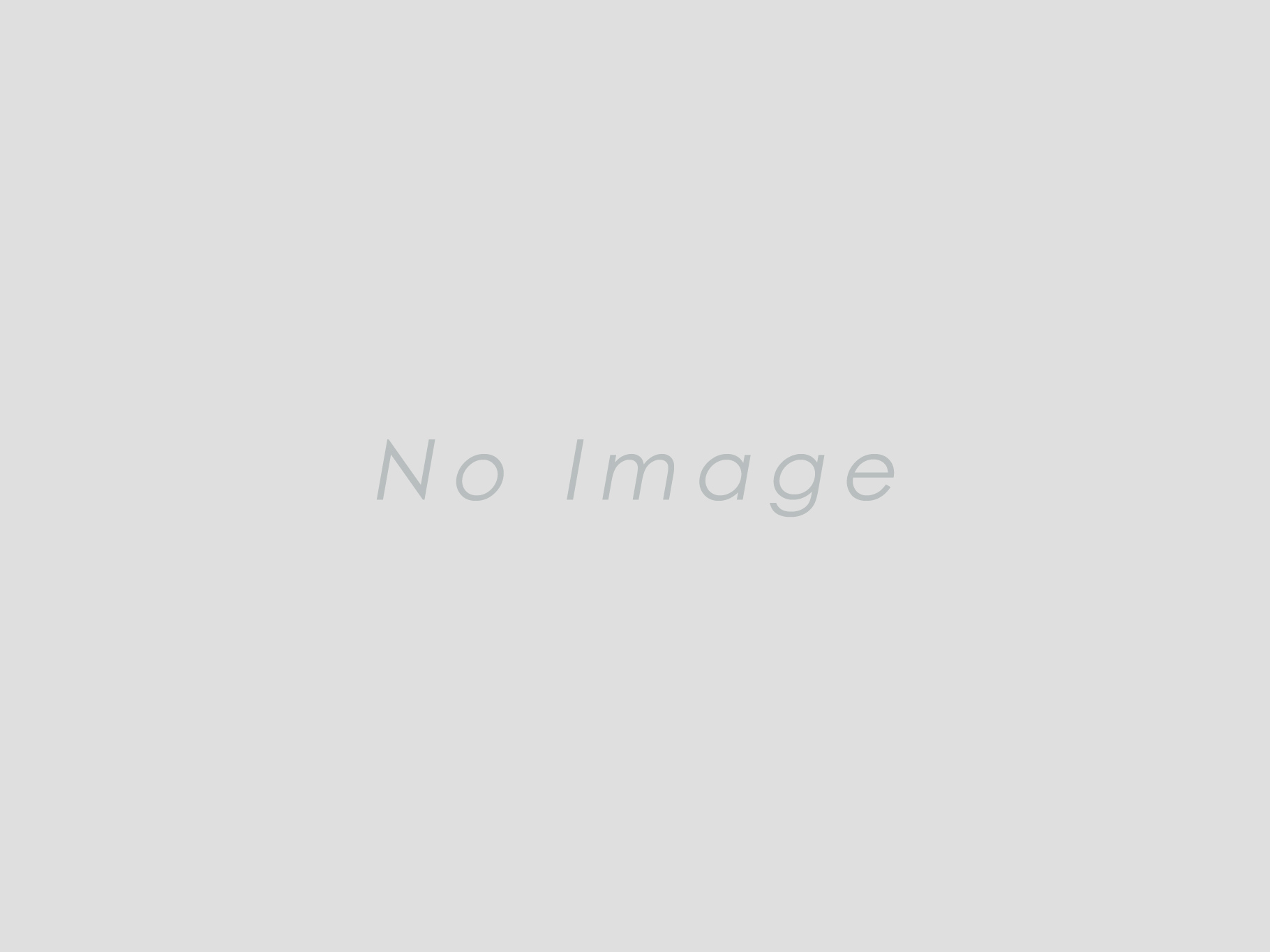
次世代レーザー機器の開発動向
次世代レーザー機器の開発は、ますます高度な技術を取り入れ、軸芯出し方法の進化を牽引しています。従来のレーザー技術では実現が難しかった微細な調整も、最新の機器を用いることでミクロン単位の精度で可能となりました。また、新しいレーザー機器は自動化されたシステムとシームレスに統合され、操作の簡便さと効率性が大幅に向上しています。これにより、産業機械のメンテナンスや調整作業が迅速かつ確実に行えるようになり、企業の生産性向上が期待されます。世界各地で進行中の開発プロジェクトでは、さらなるミニマリズムとポータビリティを追求しており、これにより現場での使用が一層便利となるでしょう。
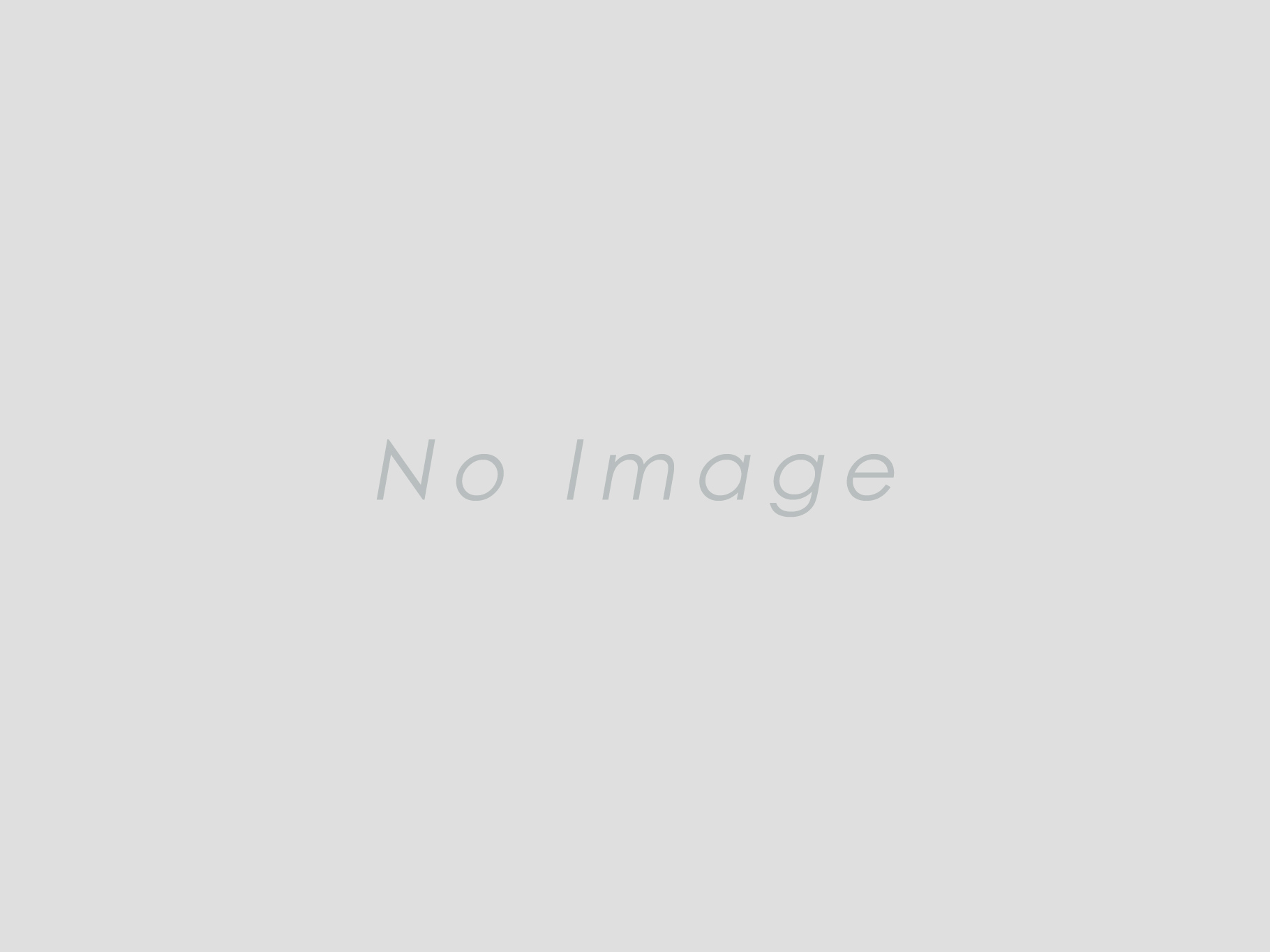
レーザー技術と自動化の融合
レーザー技術と自動化の融合は、軸芯出し方法に革命をもたらしています。自動化技術を組み合わせることにより、従来の手動調整よりもはるかに迅速で正確な軸芯出しが実現します。例えば、リアルタイムでのデータ解析機能を持つ最新のレーザー軸芯出し器は、瞬時にズレを検知し、自動的に補正を行います。このようなシステムは、オペレーターのスキルに依存せず、一貫した高精度を維持できるため、特に大量生産を行う工場において非常に有用です。さらに、AI技術の導入により、自動化されたプロセスが自己学習し、時間とともに精度と効率がさらに向上することが期待されています。これにより、企業は競争力を強化し、持続可能な成長を実現することができます。
従来の手法を超えるレーザー軸芯出しのベストプラクティス
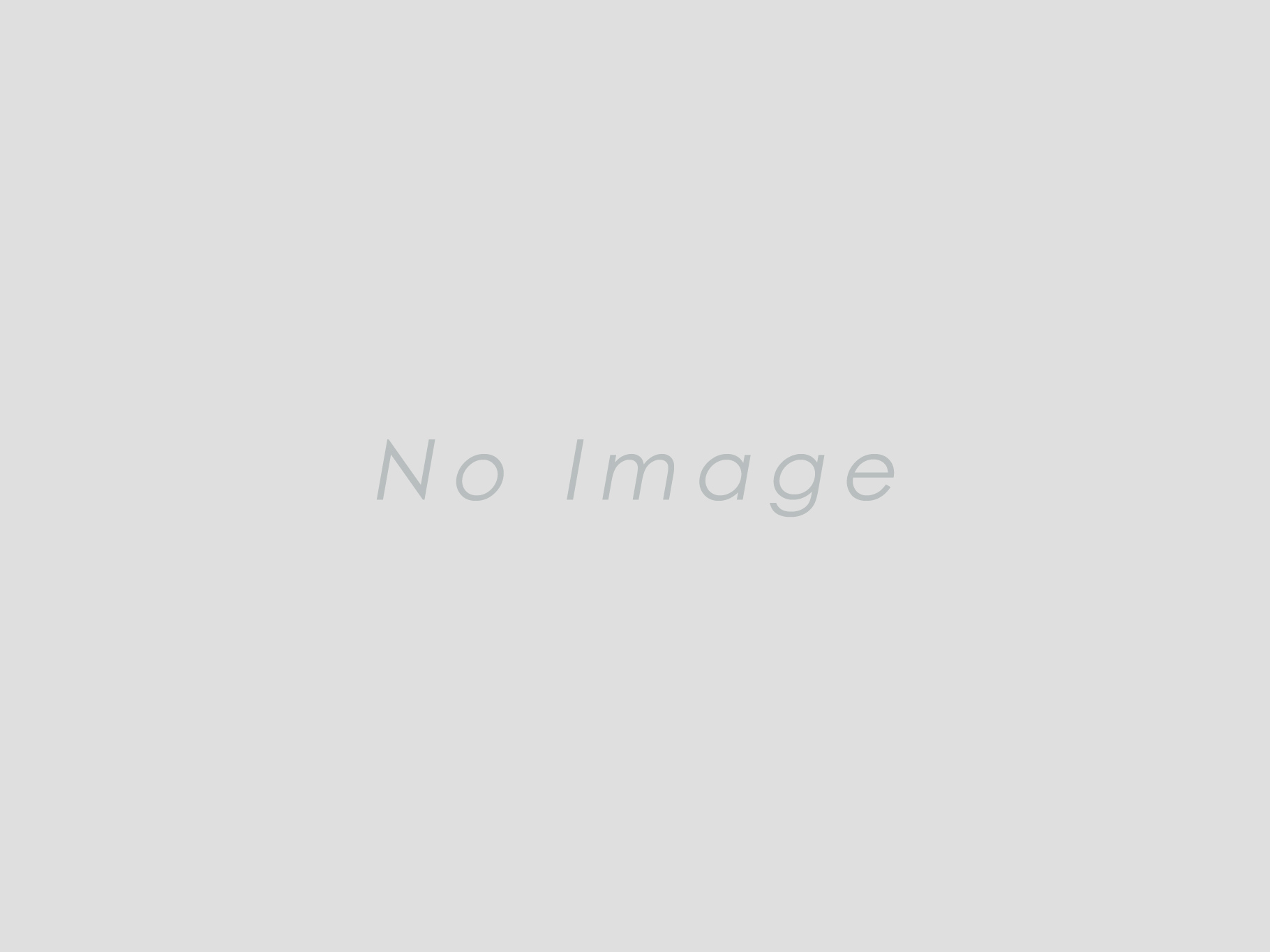
従来手法の短所とレーザー技術の長所
従来の軸芯出し方法は、手動の微調整や目視による確認が主な手段でした。この方法では、精度が低く、時間がかかる上に、作業者の専門的なスキルが必要とされました。摩擦やエネルギーロスが増加し、機械の寿命が短くなることもしばしばです。一方、レーザー技術を利用した軸芯出し方法では、ミクロン単位の高精度な調整が可能であり、作業時間も大幅に短縮されます。レーザーセンサーが迅速かつ正確に軸のズレを検出し、簡単な操作で正しい位置に調整することができます。このため、摩耗やエネルギーロスが最小限に抑えられ、機械の性能と寿命が飛躍的に向上します。
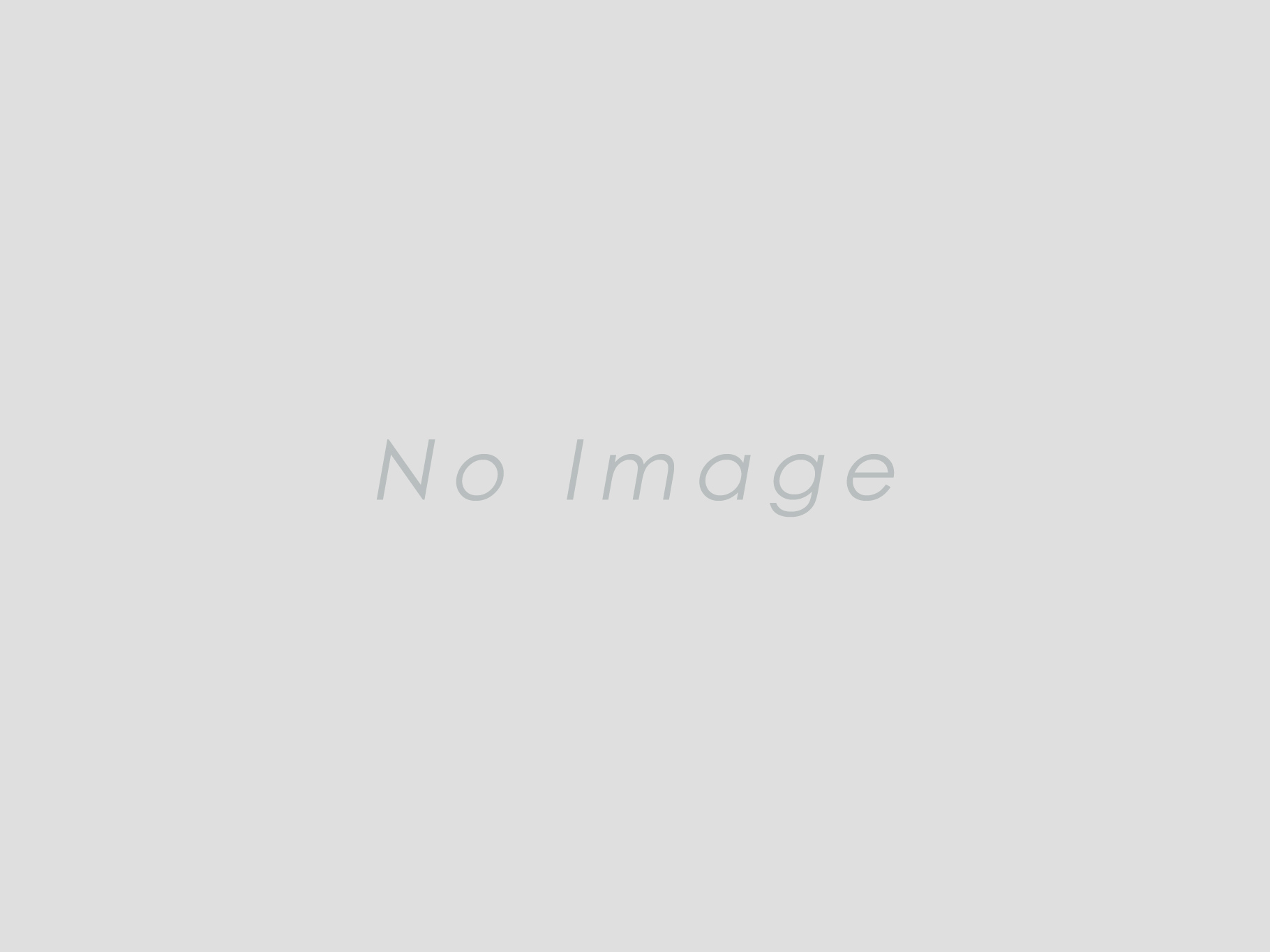
ベストプラクティス事例紹介
レーザーを用いた軸芯出し方法のベストプラクティスとして、まず初めに正確な測定機器の選定が重要です。高品質なレーザー軸芯出し器を使用することで、測定の信頼性が向上します。次に、定期的なメンテナンスと校正が必要です。これにより、測定機器の精度を保ち、継続的な高性能を確保できます。さらに、作業手順を標準化し、作業者への十分なトレーニングを実施することも重要です。これにより、操作ミスを減少させ、均一な品質の軸芯出しが可能となります。最後に、データの記録と分析を行い、問題の早期発見と対策を講じることで、効率的な運用が実現します。これらのベストプラクティスを踏襲することで、レーザー技術を最大限に活用し、高精度かつ効率的な軸芯出しが可能となります。
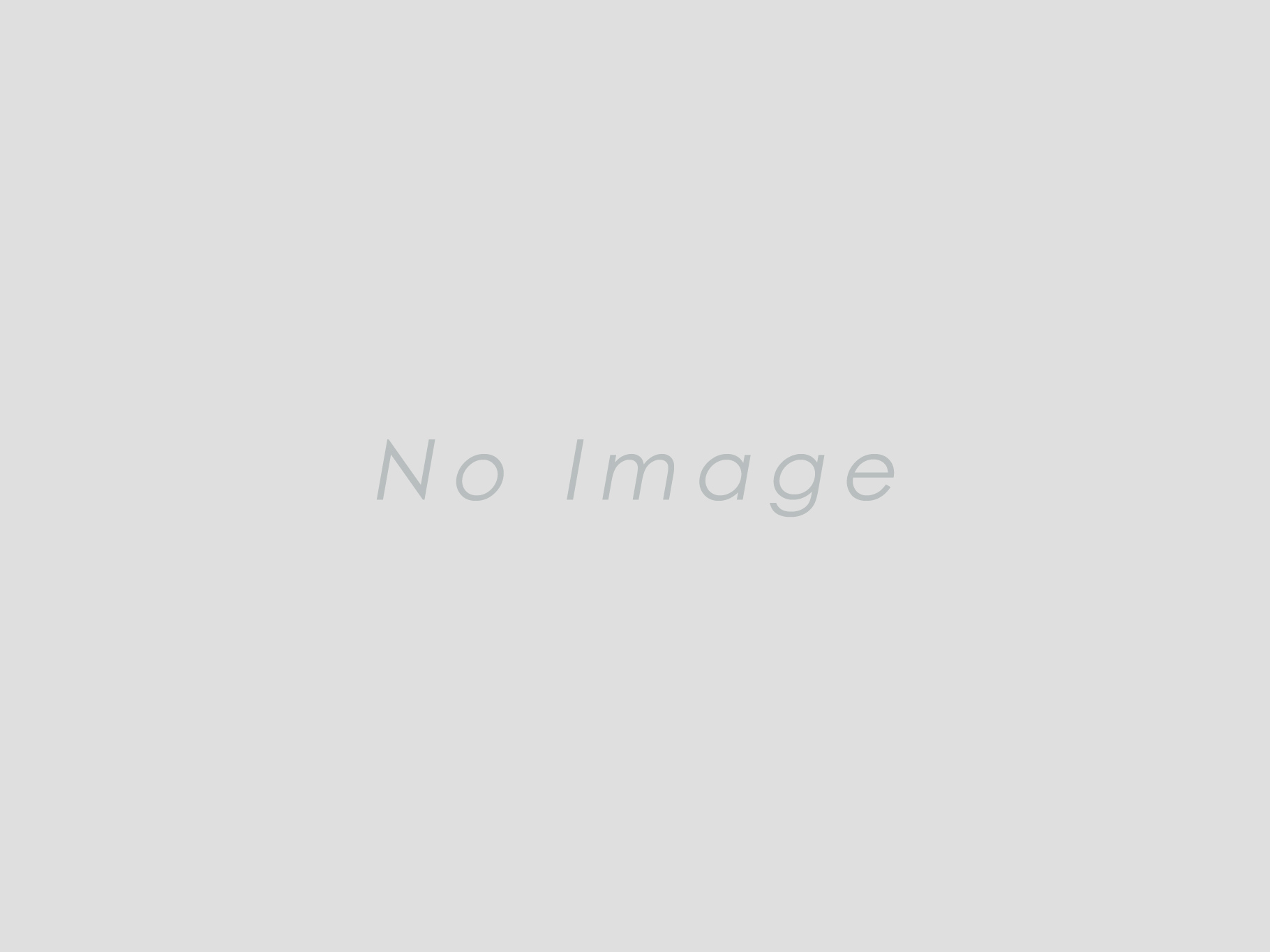
レーザー技術導入の成功事例
レーザー技術を用いる軸芯出し方法は、さまざまな企業で成功を収めています。たとえば、自動車部品メーカーでは、従来の手法では調整に多くの時間を要していましたが、レーザー技術の導入により作業時間が劇的に短縮され、生産ライン全体の効率が向上しました。また、精密機械メーカーでは、ミクロン単位の精度で軸芯を調整できるようになり、製品の品質が大幅に向上しました。これにより、顧客満足度も向上し、競争力が強化されました。
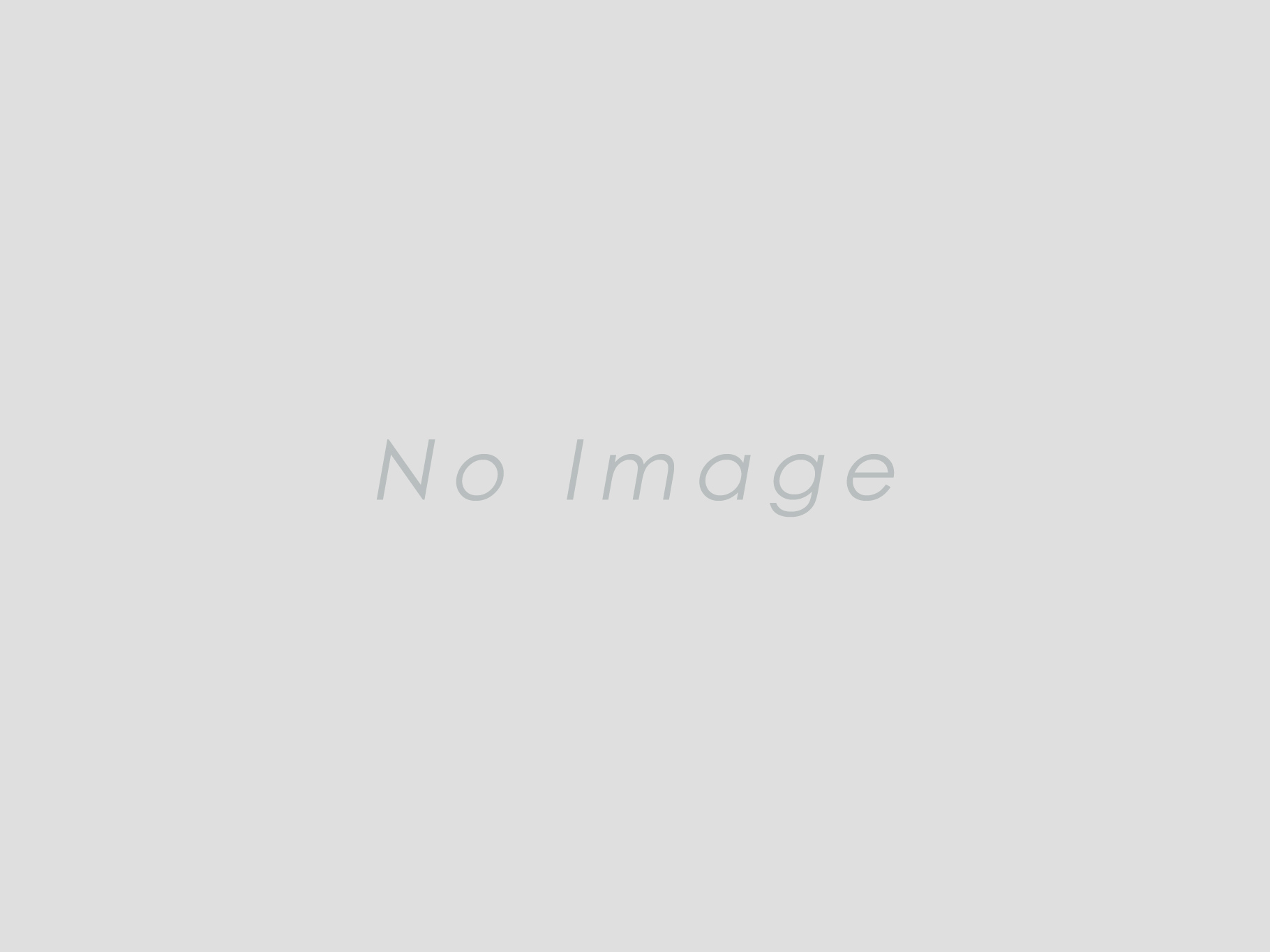
高精度・高効率の実現法
レーザーを使った軸芯出し方法は、高精度と高効率を同時に実現するための優れた手法です。まず最初に、レーザー装置を使用して対象物の位置を正確に測定します。この際、レーザー光を利用することで、非常に微細なずれまで検出可能です。その後、調整プロセスでは、測定結果をもとに迅速かつ正確に軸芯を修正します。これにより、従来の手法では考えられなかったレベルの精度が達成され、同時に作業時間も短縮されます。結果として、工場全体の生産性が向上し、エネルギー効率も最適化されます。
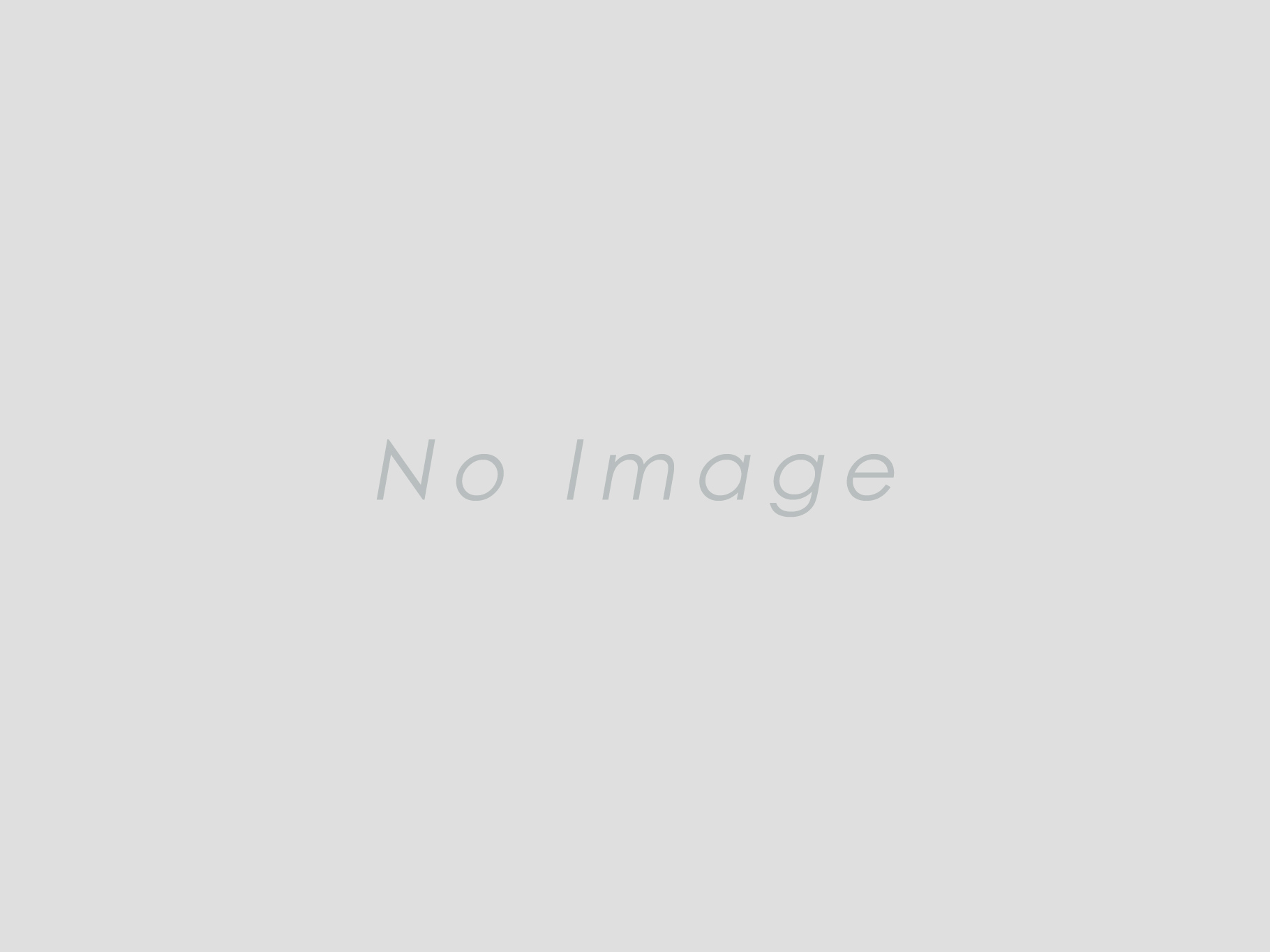
レーザー軸芯出しの導入プロセス
レーザー軸芯出しの導入プロセスは、いくつかのステップを踏むことで成功します。まず、現場の調査が必要です。これは、既存の機械設備の状態を把握し、どの部分に軸芯出しが必要かを特定するためです。次に、適切なレーザー機器の選定と購入が行われます。選定には、使用する機械の種類や規模、必要な精度が考慮されます。導入後は、操作方法や安全対策についてのトレーニングが重要です。初期の設定と調整も丁寧に行うことで、長期的な効果を最大限に引き出すことができます。最後に、定期的なメンテナンスと評価を行い、軸芯出しの精度を保つことが求められます。これらのステップを踏むことで、レーザー軸芯出しの効果を最大限に活用することができます。
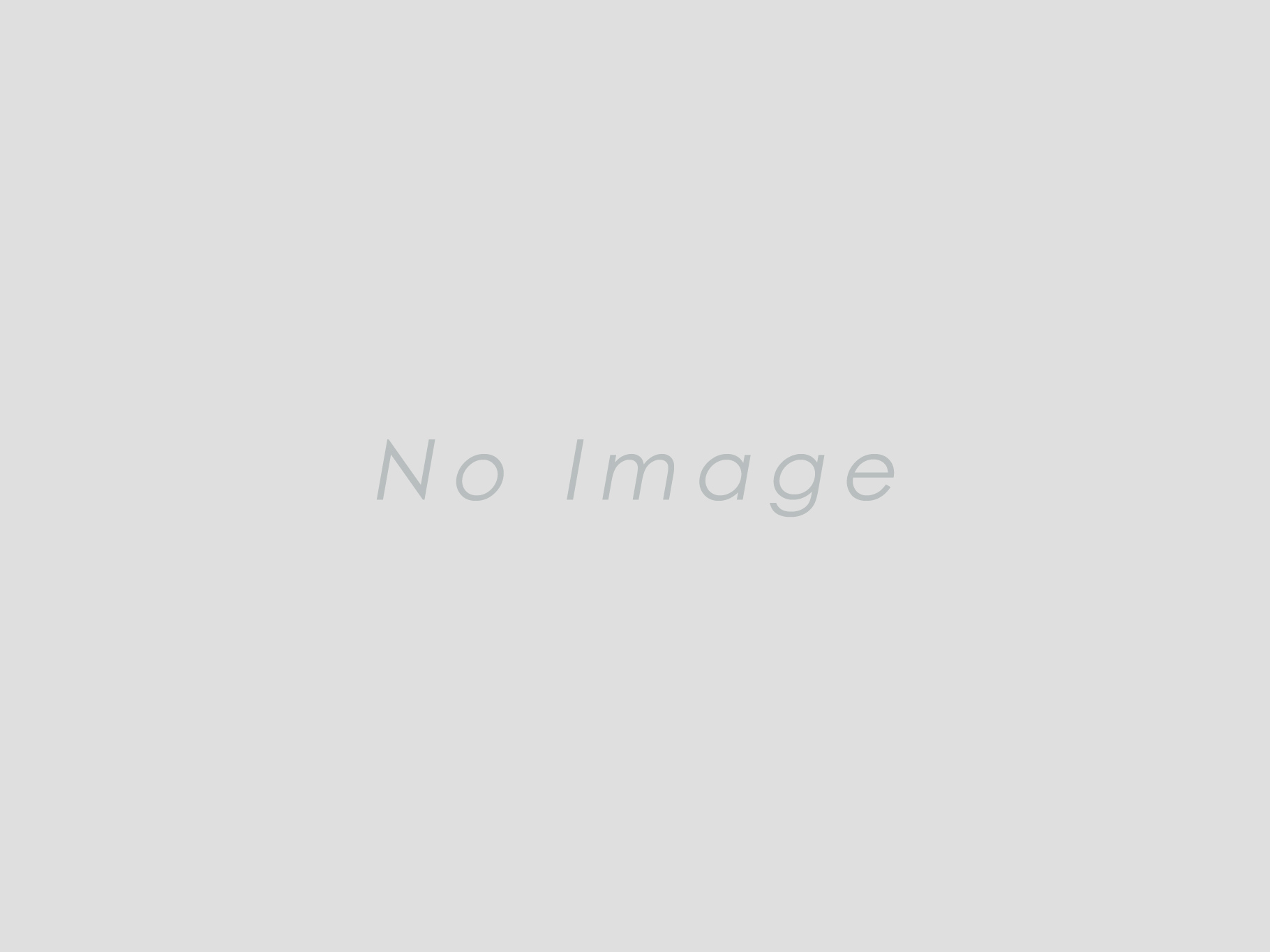
レーザー技術と品質管理の重要性
レーザー技術を用いた軸芯出しは、品質管理においても重要な役割を果たします。まず、レーザー技術は高い精度を誇り、ミクロン単位の誤差を許容しないため、機械の効率と耐久性が向上します。これにより、生産ラインの安定性が確保され、製品の品質が一貫して高い状態を維持できます。また、レーザー技術は迅速な調整を可能にするため、ダウンタイムを最小限に抑え、生産性の向上に寄与します。さらに、異常摩耗や機械故障のリスクを低減し、保守コストの削減にもつながります。品質管理の観点から見ても、レーザーを用いた軸芯出しは、製造業における競争力を高めるための重要な技術です。このように、レーザー技術は生産効率と品質管理の両面で大きなメリットをもたらします。
短時間で高精度を実現するレーザーによる軸芯出しの方法
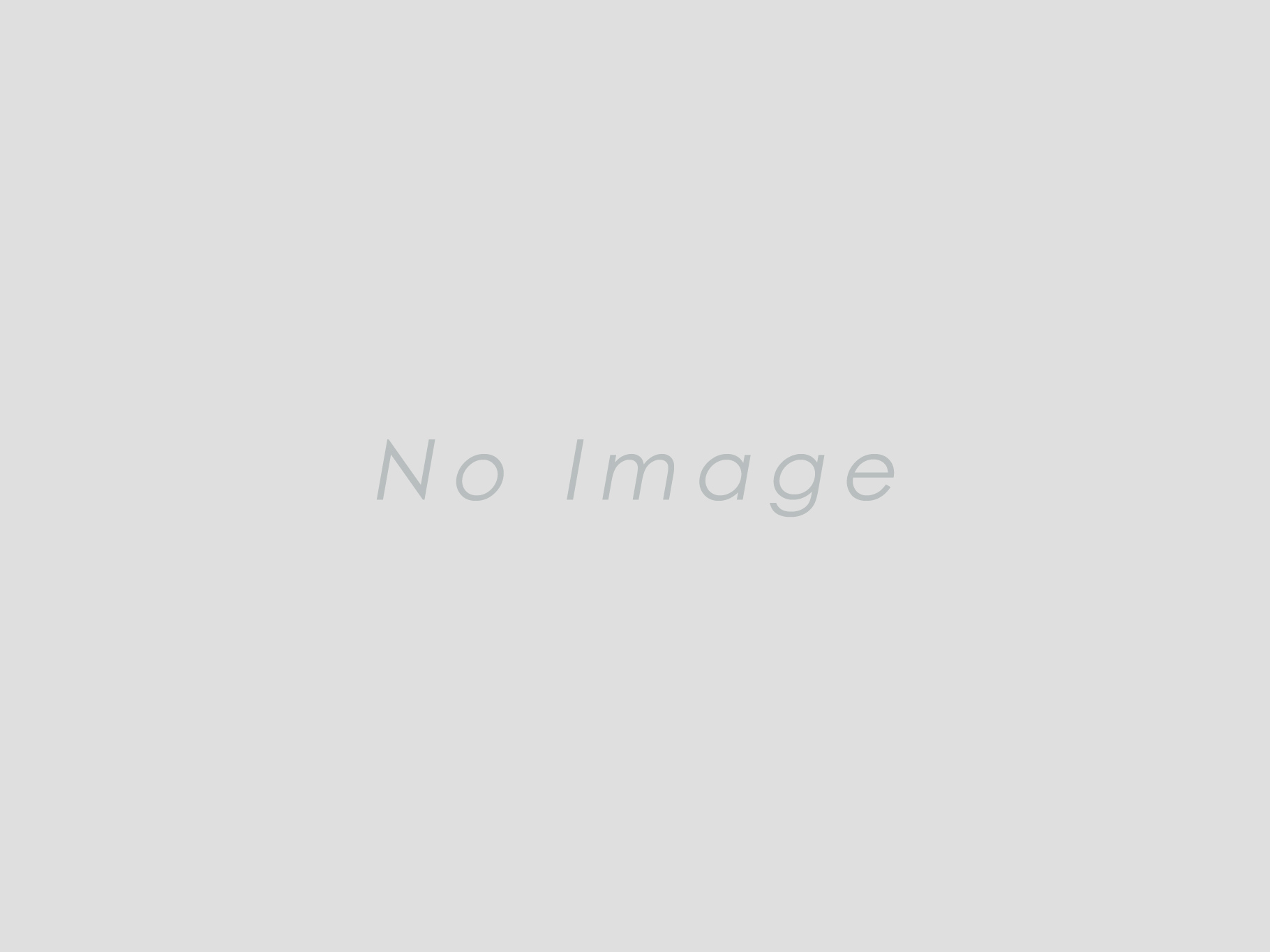
短時間での軸芯出しの秘訣
レーザーを用いた軸芯出し方法は、その精度と効率の高さから、従来の手法に比べて大幅な時間短縮が可能です。まず、レーザーの設置とキャリブレーションに注意を払いましょう。正確な位置にレーザーを設置し、事前にキャリブレーションを行うことで、作業開始から終了までの時間を最小限に抑えることができます。次に、レーザーの照射範囲と対象の確認です。作業対象が明確であれば、無駄な調整時間を省くことができます。また、レーザー機器の利用には、事前準備と技術的な知識が必要です。これにより、作業の流れがスムーズになり、短時間での軸芯出しが実現します。最終的に、軸芯出しの工程をしっかりと理解し、効率的に進めることが、短時間での高精度な軸芯出しの秘訣です。
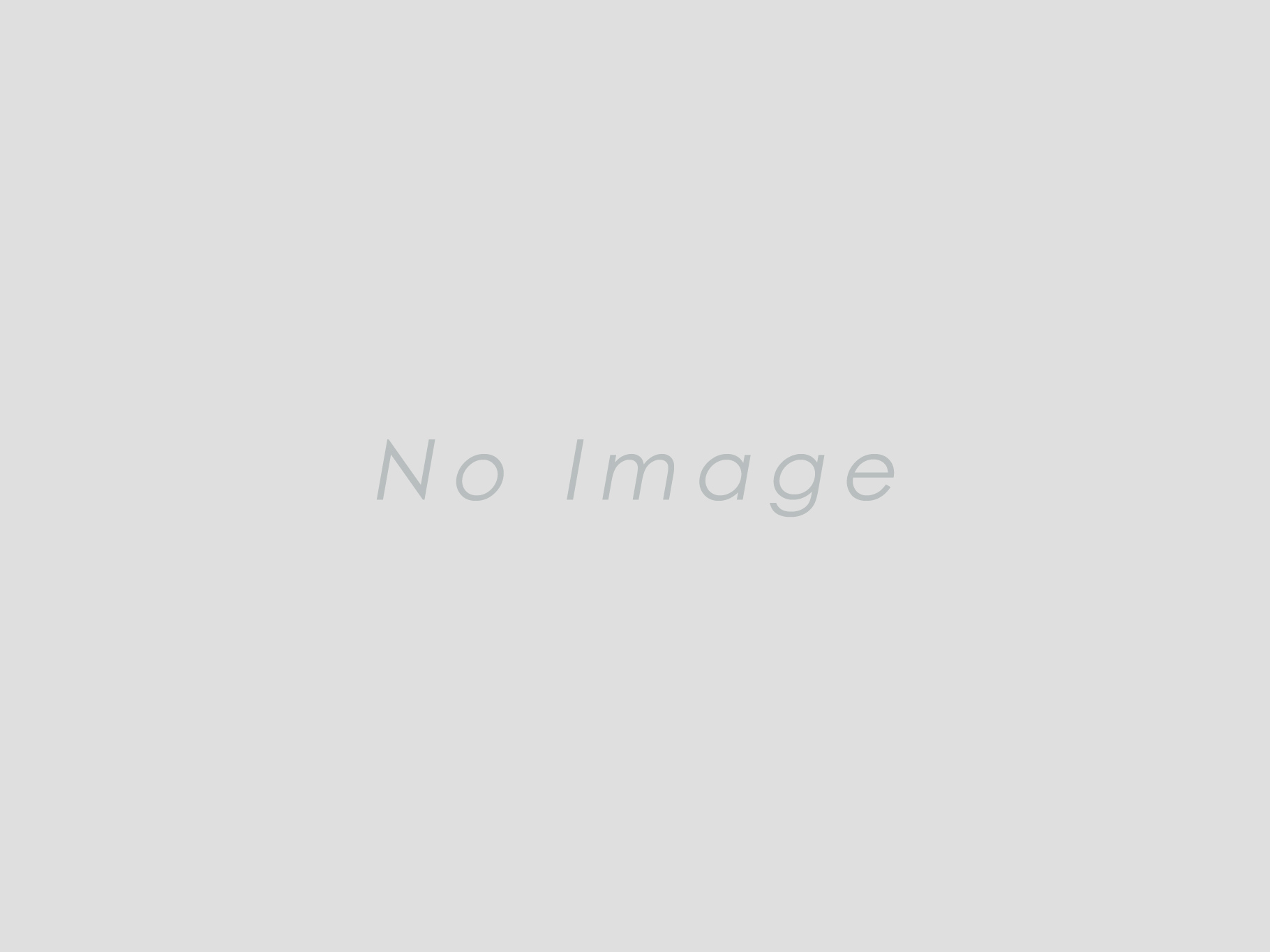
高精度実現の具体的手法
高精度な軸芯出しを実現するための具体的な手法には、いくつかの重要なポイントがあります。まず、レーザー機器の正確な設置が不可欠です。レーザーの位置をミクロン単位で調整し、機械の軸芯に対して正確に照射されるようにします。次に、レーザーの波長と出力を適切に設定することが大切です。これにより、計測の誤差を最小限に抑えることができます。また、温度や振動などの環境要因も考慮する必要があります。これらの要因が精度に影響を与えることがあるため、作業環境を整えることも重要です。さらに、測定データの解析と微調整を行い、軸芯のズレを最小限に抑えます。最後に、これらの手法を組み合わせて一貫したプロセスを確立することで、高精度な軸芯出しが実現します。
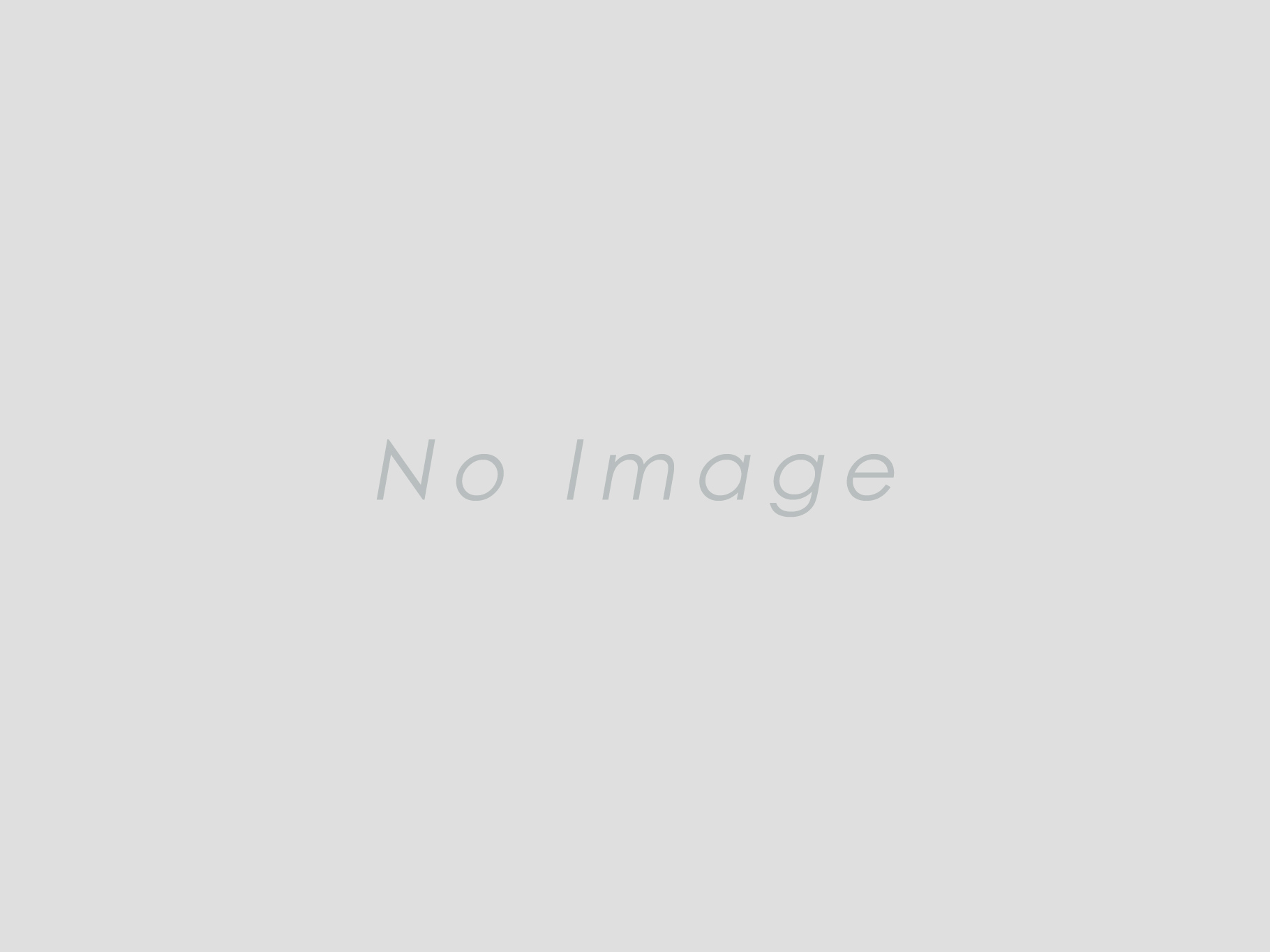
レーザー技術導入のステップ
レーザーによる軸芯出し方法を導入する際には、まず適切な機材の選定が重要です。レーザー光源の種類や精度、測定範囲などを考慮し、最適な機材を選びます。次に、使用するソフトウェアの設定とキャリブレーションを行います。これにより、測定結果の精度が大幅に向上します。さらに、操作方法の習得と定期的なメンテナンスを行うことで、長期間にわたり高精度な軸芯出しが可能となります。このようなステップを踏むことで、レーザー技術の持つポテンシャルを最大限に引き出すことができます。
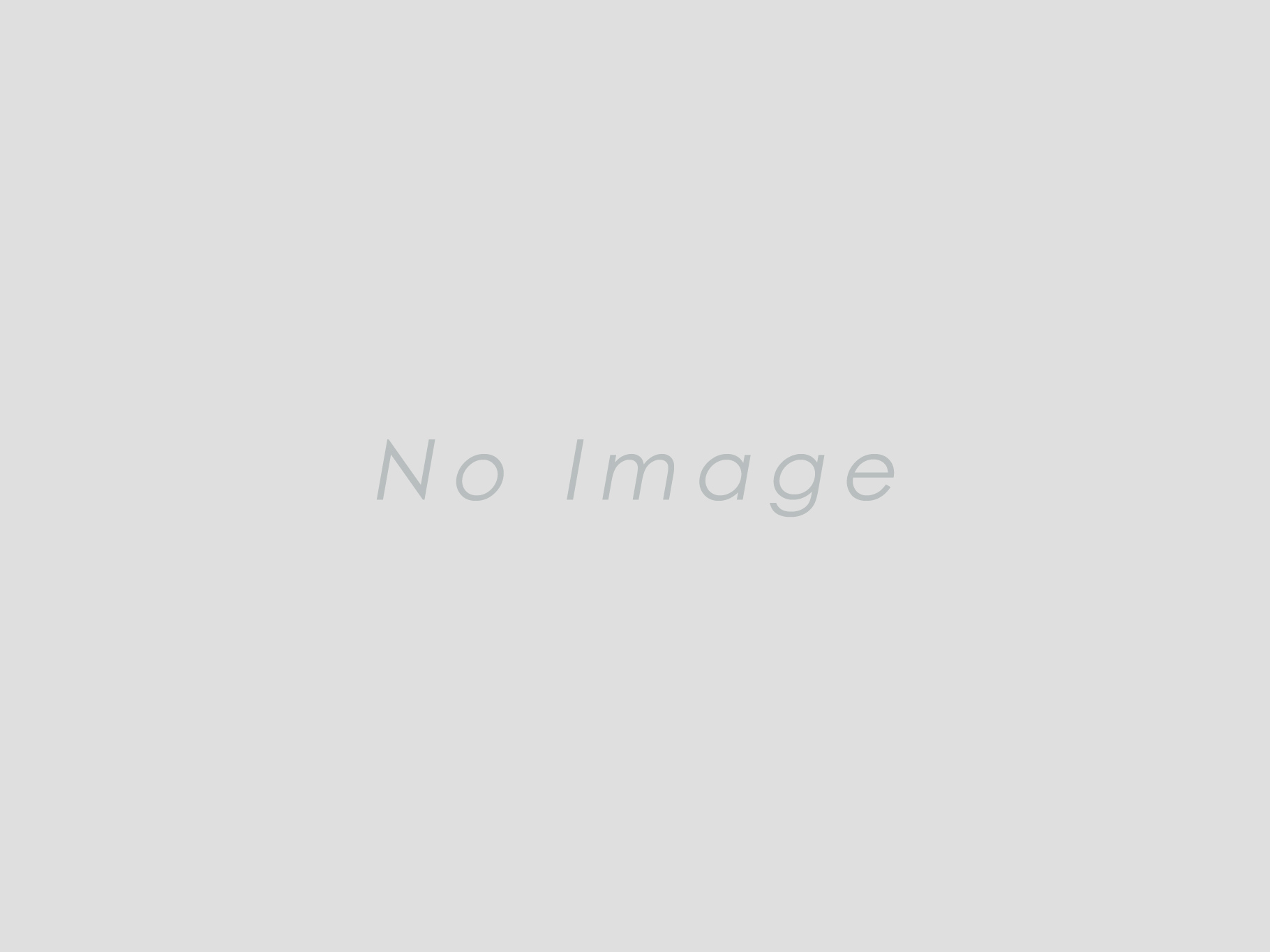
短時間での高精度を支える技術
レーザー軸芯出し方法の大きな利点は、その短時間で高精度な調整が可能な点です。レーザー光を用いることで、機械の微小なズレを迅速かつ正確に検出できます。これにより、従来の手法では時間がかかる作業も、わずかな時間で完了します。さらに、デジタル技術との組み合わせにより、リアルタイムでのデータ解析やフィードバックが可能となり、調整作業の精度が一層向上します。この技術が支える高精度と短時間の実現は、現代の産業界において非常に価値があります。
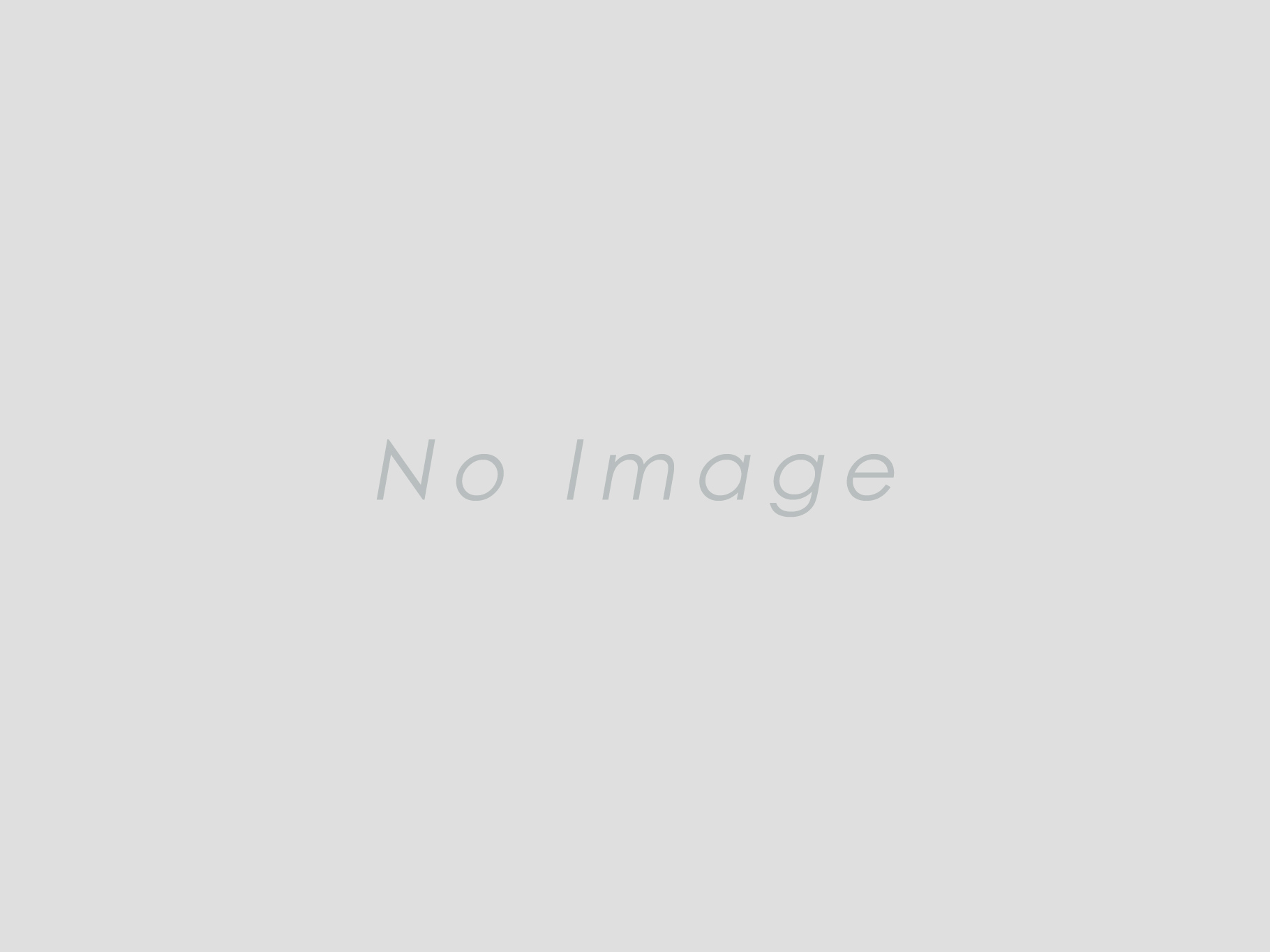
作業効率の向上法
レーザー技術を用いた軸芯出し方法は、作業効率の向上にも大きく貢献します。従来の手法に比べ、短時間で高精度な調整が可能となり、機械の稼働時間を最大限に活用できます。これは、レーザー光の特性を活かした高精度測定によって実現されます。さらに、操作が容易であるため、特別な技術や長時間の訓練が不要です。このような効率的な作業方法は、企業全体の生産性向上に直結します。また、レーザー軸芯出し器の導入により、作業者の負担が軽減され、安全性も向上します。これにより、長期的な視点でのコスト削減が期待でき、企業の競争力を高める要因となります。
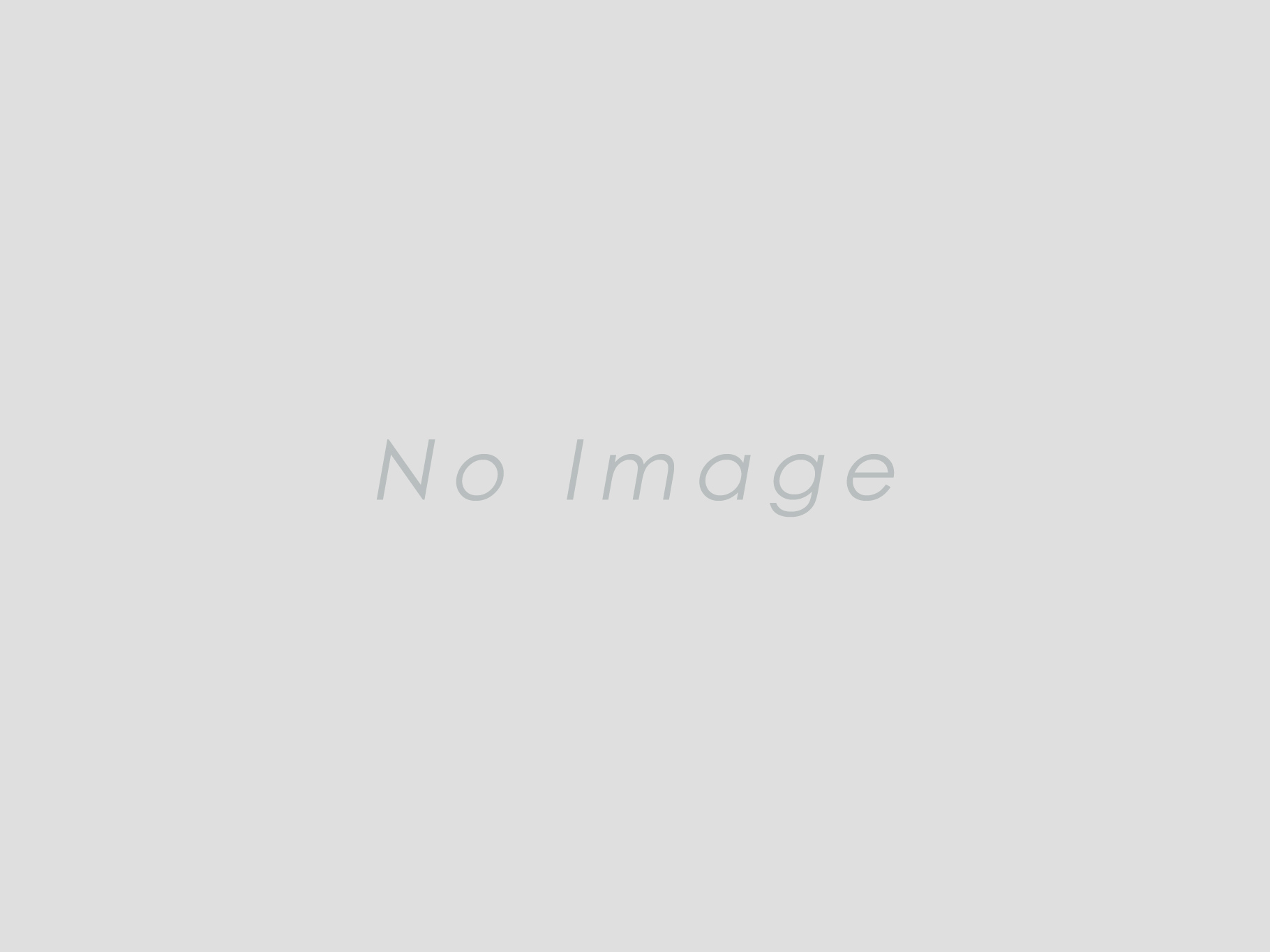
レーザー技術を用いた迅速な軸芯出しの実例
レーザー技術を活用した軸芯出しの具体的な実例を通じて、その効果を確認しましょう。例えば、ある製造業の企業では、従来の手法で軸芯出しに2日間を要していましたが、レーザー軸芯出し器を導入したことで、わずか数時間で作業を完了することができました。この結果、機械の稼働時間が大幅に延び、生産ライン全体の効率が向上しました。また、ミクロン単位の高精度な調整が可能となり、機械の振動や摩擦が減少し、メンテナンスの頻度も低減されました。このように、レーザー技術を用いることで、短時間での高精度な軸芯出しが実現し、企業の競争力を高めることができます。次回は、更なる最先端技術の応用についてご紹介しますので、ぜひご期待ください。